反芻リジッドフレックス-パート2
フレキシブルやリジッドフレキシブル基板はどのように製造されるのでしょうか?このブログでは、どのように材料を組み合わせ、ラミネート処理し、切り取って最終製品を作り上げるかについて解説します。
リジッドフレキシブルについての解説:第2部
フレキシブルやリジッドフレキシブル基板はどのように製造されるのでしょうか?このブログでは、材料をどのように組み合わせ、ラミネート処理し、切り取って最終製品を作り上げるのかについて解説します。
フレキシブルとリジッドフレキシブルの製造プロセス
前回のブログでは、リジッドフレキシブル基板についての解説の第1回として、自由に曲げられる基板を製造するために使用される材料について解説しました。前回予告したように、第2回目のブログではそれらの材料をどのように組み合わせ、ラミネート処理し、切り取って最終製品を作り上げるのかについて解説します。来週は、これらの手順全てを検討し、関連する設計上の課題について説明します。
フレキシブル基板のビルドアップ
一般的なフレキシブルやリジッドフレキシブルの基板は、最初は単純なものに見えます。しかし、これらの基板はその性質上、構築プロセスにいくつかの追加手順を必要とします。リジッドフレキシブル基板は常に、片面、または両面のフレキシブル層から始まります。先週述べたように、製造業者はラミネート済みのフレキシブル、または未加工のPIフィルムを使用し、最初の被覆として銅箔でラミネートまたはメッキ処理します。フィルムのラミネートには粘着性の薄い層が必要です。これに対して接着剤なしの被覆には銅の「シード」レイヤーが必要です。このシードレイヤーは最初に蒸気付着技法 (スパッタリング) を使用して塗布され、その上に化学的に付着された銅箔をメッキするための鍵となります。この片面または両面のフレキシブル回路に、リジッド基板の一般的な両面コアとほぼ同じ手順でドリル加工、スルーメッキ、エッチングが行われます。
フレキシブルの製造手順
次のGIF動画は、フレキシブル回路の作成手順を、一般的な両面フレキシブル回路について示したものです。
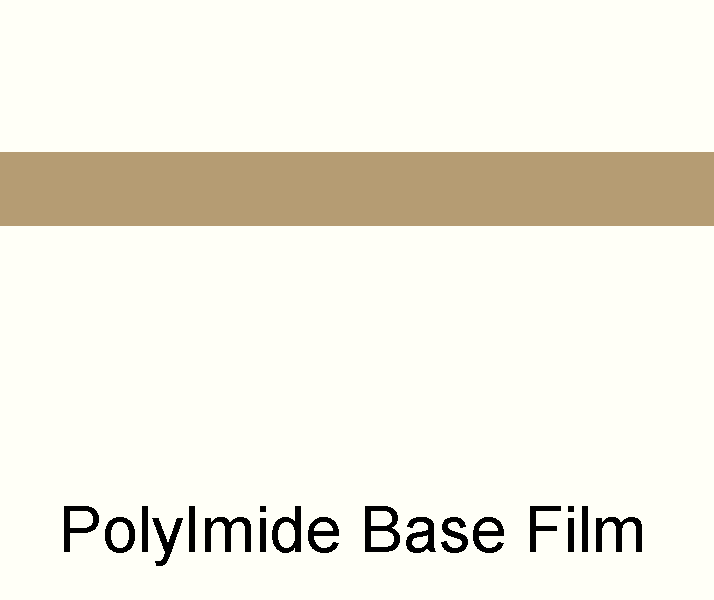
図1:フレキシブル回路のビルドアップ プロセスを示すGIF動画
1. 接着剤/シード コーティングの塗布
エポキシ、またはアクリルの接着剤を塗布するか、スパッタリングを使用して、メッキ用の銅箔層を作成します。
2. 銅箔の追加
RA/ED銅箔ラミネーションをシード層に接着(より一般的な手法)、または化学的にメッキします。
3. ドリル加工
ビアとパッドの穴は、ほとんどの場合に機械的にドリル加工されます。複数のメッキされたフレキシブル基板は、複数のリールから組み合わせ、作業プレート間でドリル加工し、ドリル加工機械の反対側にある別のリールにロールアウトするという方法で同時にドリル加工されます。切り取り済みのパネルは、リジッドコアと同様に組み合わせてリジッドブランク間でドリル加工できますが、より注意深い登録が必要で、位置合わせの精度も低下します。非常に小さな穴の場合はレーザーによるドリル加工も使用できますが、それぞれの薄膜を別にドリル加工する必要があるため、コストが大幅に上昇します。高精度が必要な場合(マイクロビア)はエキシマ (紫外線)、またはYAG(赤外線)レーザー、中程度の穴(4mil以上)ではCO2レーザーが使用されます。大きな穴やカットアウトはパンチで穴開けしますが、これは別の処理手順になります。
4. スルーホールメッキ
穴を開けた後で、リジッド基板のコアと同じように銅箔が付着、および化学的にメッキされます。
5. エッチング抵抗印刷
感光性エッチング抵抗が薄膜の表面にコーティングされ、目的のマスクパターンを使用して露出を行い、銅箔の化学的なエッチングの前に抵抗が作成されます。
6. エッチングとストリッピング
露出が行われた銅箔のエッチングの前に、エッチング抵抗はフレキシブル回路から化学的にストリッピングされます。
7. カバーレイ
フレキシブル回路の上端と下端の領域は、指定の形に切り取られたカバーレイによって保護されます。フレキシブル回路のセクションにコンポーネントが実際に取り付けられることもあり、その場合はカバーレイがソルダーマスクとしても機能します。カバーレイの最も一般的な材質は接着剤付きの追加のポリイミド薄膜ですが、接着剤なしのプロセスも使用可能です。接着剤なしのプロセスでは、感光性のソルダーマスク(リジッド基板のセクションに使用されるものと同じ)が使用され、本質的にはカバーレイがフレキシブル回路に印刷されます。より精度の低い安価な設計では、スクリーン印刷とUV露出による最終的な硬化も選択可能です。
図2: カバーレイ付きのフレキシブル回路の例 - カバーレイの開口部は一般にコンポーネント パッドよりも小さいことに注意してください。
カバーレイについての重要な注意は、これが一般に、フレキシブル回路上で最終的に露出する部分にのみ配置されるということです。リジッドフレキシブル基板の場合、カバーレイはリジッドセクションには、小さな(通常は約1/2mm程度の)オーバーラップを除いて配置されません。カバーレイをリジッドセクション全体に含めることもできますが、リジッド基板の接着性やz軸の安定性に悪影響を及ぼします。この種の選択的カバーレイは絶対に必要な部分のみをカバーするため、このプロセスを使用する基板製造業者からは「ビキニカバーレイ」と呼ばれます。また、カバーレイのコンポーネントや接続パッドの切り取りでは、パッドのランドの最低でも2つのサイドが、下にアンカーを付けるため残されます。この点については、次回のブログで再度説明します。
8. フレキシブルのカットアウト
フレキシブル基板を作成する最後の手順はカットアウトです。これは多くの場合に「ブランク処理」と呼ばれます。ブランク処理を大量に行うには、油圧パンチとダイセットを使用するのが費用対効果の大きい方法ですが、この方法では工具のコストがかなり高価になります。しかし、この方法を使用すると多くのフレキシブル基板を同時にパンチ加工できます。プロトタイプや少量の生産では、ブランク処理ナイフが使用されます。ブランク処理ナイフは基本的には非常に長い剃刀で、フレキシブル基板の外形の形状に曲げられ、裏打ち基板(MDF、合板、またはテフロンなどの厚いプラスチック)に刻み込まれたスロットに固定さマス。その後で、フレキシブル基板がブランク処理ナイフに押し付けて切り取られます。さらに少量のプロトタイプ作成には、X/Yカッター(ビニール標識を作るとき使用されるのと同じようなもの)も使用できます。
ラミネーションと配線
フレキシブル基板がリジッド/フレキシブルの複合スタックアップの一部を形成する場合 (ここで解説する構造)、プロセスはここで終了しません。ここまでで、リジッド部分の間に積層する必要のあるフレキシブル回路が完成します。これは個別にドリル加工、メッキ、エッチングされたコア層のペアと同じですが、はるかに厚く、ガラス繊維が含まれていないため柔軟です。しかし、前に述べたように、対象のアプリケーションによってはPIとガラスを使用して、柔軟性の低いレイヤーを作成することもできます。これはリジッド部分と積層されるため、最終的にはパネルに収め、リジッド基板のパネル部分と合わせる必要があります。
積層スタックアップ
フレキシブル回路はリジッドや他のフレキシブル部分とともにパネルに積層され、さらに接着剤が追加され、熱と圧力が加えられます。複数のフレキシブル部分が互いに隣接して積層されることはありません。これは一般に、それぞれのフレキシブル部分は柔軟性を維持するため、銅箔層が最大で2層ということを意味します。これらのフレキシブル部分は、リジッドなプリプレグとコア、またはPIボンディング シート、およびエポキシ、またはアクリル接着剤により分離されます。
本質的に、各リジッド パネルは別々の領域にルーティングされ、これらの領域ではフレキシブル部分を曲げられるようになります。
2つの2層フレキシブル回路が3つのリジッドセクションの間に埋め込まれ、リジッドフレキシブル基板として積層する例を次に示します。レイヤーのスタックアップは図3と4に示すようなものになります。
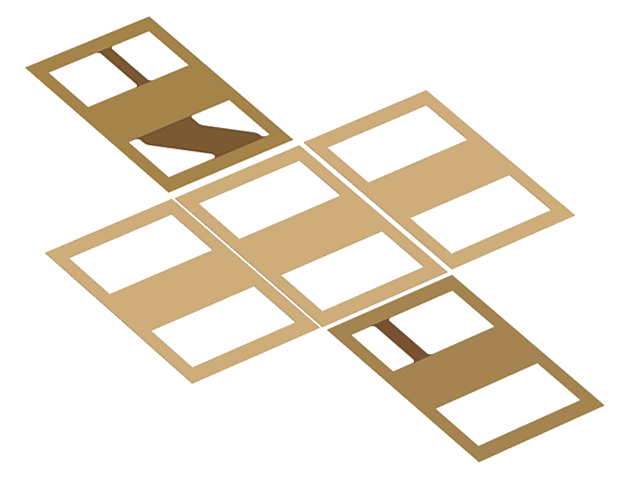
図3: エッチング、メッキ、カバーレイ、ブランクのフレキシブルパネルと、ガラスエポキシのリジッドパネルとが図のように組み合わせられます。
図4: 各フレキシブルセクションのメッキスルーホールと、リジッドセクションの最終的なメッキスルーホールを含む詳細スタック図。
図4に示すスタックアップの例では、事前にエッチングされ切り取られたフレキシブル回路が2つあり、どちらも両面で貫通メッキされています。フレキシブル回路は、フレーミング用のボーダーを含めて、最終的なアセンブリパネルにブランクされます。これにより、フレキシブル回路はリジッドパネルセクションとラミネーション後の最終アセンブリ時に平坦に維持されます。フレキシブル回路のエルボー部の支持が不十分、または開いている大きなセクションが存在すると、アセンブリ時に多少の破損の危険があります。特に、リフローオーブンの熱で問題が発生する危険性は大きくなります。次回のブログで設計の観点について解説するとき、これらの問題点のいくつかに言及します。
カバーレイも貼付されます。これは接着剤でステッカーのようにラミネートされるか、前に述べた写真印刷法で行われます。この6層スタックアップの最終的なフレキシブルおよびリジッドパネルが組み合わせられた後で、再外層(上端と下端)の最終的な銅箔レイヤーがラミネートされます。その後で、上端から下端までの貫通メッキされる穴のドリル加工が別に行われます。レーザードリル加工のブラインドビア(上端から最初のフレキシブルまで、下端から最後のフレキシブルまで)を作成することもできますが、これも設計のコスト増になります。
最後の手順は、上端と下端のソルダーマスク、上端と下端のシルクスクリーン、および保護メッキ(ENIGなど)または熱風レベラー加工(HASL)の印刷です。
物理的制約
複数のフレキシブルサブスタック
リジッドとフレキシブルのセクションから、ほとんどのスタックアップを構築可能ですが、関係する製造手順と材料の性質を十分に考慮しないと製造が非常に高価になる可能性があります。フレキシブル回路について留意しておくべき重要な要素の1つは、回路が折り曲げられるとき材質内に発生する圧力です。この場合も、銅は繰り返しまたは小さな半径で折り曲げられることで硬化し、やがて疲労破断が起きることが知られています。この問題を軽減する方法の1つは、シングルレイヤーのフレキシブル回路のみを使用することです。この場合、図5に示すように銅箔は折り曲げ半径中央値の中央に位置するため、薄膜基板とカバーレイが最大の圧縮および引っ張りを受けることになります。ポリイミドは非常に弾力性があるため、これは問題とならず、繰り返し移動を行った場合の寿命が複数の銅レイヤーよりもはるかに長くなります。
図5: 折り曲げが多く発生する回路の場合、シングルレイヤーフレキシブルにRA銅箔を使用して、回路内の銅箔の疲労寿命(障害が発生するまでの折り曲げ回数)を増やすのが最良です。
同様の方法として、複数の別のフレキシブル回路も多くの場合に必要となりますが、重なっているセクションでフレキシブルセクションの長さにより折り曲げ半径が制限される場所を曲がり目にすることは避けることをおすすめします。設計に関するこれらの考慮事項については、次回の記事でさらに詳しく解説します。
接着性ビーズ
前回述べたように、フレキシブル回路がリジッド基板から出ていく部分で補強材の使用の検討が必要なことがあります。エポキシ、アクリル、またはホットメルトのビーズを追加すると、アセンブリの寿命を延ばすため役立ちます。しかし、これらの液体を塗布して硬化させる場合、製造プロセスに面倒な手順が加わることになります。
液体の自動塗布を使用することもできますが、接着剤の塊がアセンブリの下に垂れることがないよう、アセンブリ技術者と十分注意して共同作業を行う必要があります。場合によっては接着剤を人手で塗布する必要があり、さらに時間とコストが必要です。いずれの場合も、製造やアセンブリの担当者に明確なドキュメントを渡す必要があります。
補強板と終端
フレキシブル回路の最終端は一般に、メインのリジッド基板アセンブリに接続するのでなければ、コネクタが接続されます。このような場合、終端に補強板(接着剤付きの厚いポリイミド)またはFR-4を貼付できます。この場合、一般に、フレキシブルの終端はリジッドフレキシブルセクション内にも埋め込んだ状態にするのが便利です。
パネル
リジッドフレキシブル回路はアセンブリプロセスのためパネル内に維持されるので、リジッドな終端にコンポーネントを配置して半田付けできます。一部の製品では、フレキシブル部分の一部の領域にもコンポーネントの取り付けが必要となり、この場合はアセンブリ時にフレキシブル部分を支持するため、パネルに追加のリジッド領域を取り付ける必要があります。これらの領域はフレキシブルに接着されず、深さのコントロールされたルータービット(「マウスバイト」付き)で外にルーティングされ、最終的にアセンブリ後にパンチ加工されます。
図6: 最終的なリジッドフレキシブルパネルの例。この例には前面および背面の基板エッジとフレキシブル回路があり、外にルーティングされていることに注意してください。リジッド側はV字型の溝が付けられており、後で切り離されます。これにより、筐体への組み込みの時間を節約できます。
まとめ
今回の内容では、リジッドフレキシブル基板の製造プロセスの概要について軽く触れただけです。しかし、製造プロセスがどのようなものかについては理解していただけたと思います。次回のブログでは、これらの製造と成功に大きく影響する設計上の考慮事項の多くについて解説します。
皆様の参考になったことを期待しますが、ここでは述べ足りないことも数多く存在します。コメントやご質問は自由にお寄せください。また、リジッドフレキシブルPCBの設計について経験したことがおありなら、ぜひお聞かせください。皆様の声をお待ちしております。
今すぐAltium Designerの無償評価版をリクエストして、世界最高のPCB設計ソリューションをお試しください!ご不明な点などございましたら、お問合せフォームにご入力ください。