Cap sur l’intégration mécanique (partie 4)
-68354.jpg)
1. Introduction
Le deuxième article de cette série présentait un projet de convertisseur statique utilisable en autonomie ou comme brique de base d’un convertisseur plus complexe – comme un onduleur triphasé par exemple – intégrant les composants de puissance (IGBTs), leurs drivers isolés et des capteurs (de tension/courant/température) ainsi qu’un microcontrôleur assurant le monitoring (protection), l’interface homme/machine (IHM) et éventuellement le contrôle MLI. Une première version a été présentée ici et a mis en évidence l’intérêt d’une modélisation 3D pour un prototype virtuel afin de garantir l’intégration en boîtier. Toutefois, la problématique du coût a aussi été évoquée avec des contraintes très différentes des divers constituants du système (besoin d’isolation en haute tension, pistes larges et de forte épaisseur pour les forts courants, densité forte de composants pour la partie « microcontrôleur » incluant des alimentations à découpage – plusieurs rails d’alimentation requis – les plus compactes possibles). C’est pourquoi une deuxième version “multi-PCB” a été retenue :
- « contrôle / IHM » en 4 couches (35 µm),
- « driver + mesure de température » en 2 couches (35 µm),
- « busbar de puissance » en 2 couches (70 µm),
- « mesure de courant » en 2 couches (70 µm),
- « mesure de tension DC » en 2 couches (35 µm),
- carte(s) simple face support(s) pour ventilateur(s) optionnels.
Les cartes ont aussi été conçues pour éliminer toute fabrication de pièce spécifique (pas d’impressions 3D comme pour la première version) en permettant
- soit l’assemblage des cartes sur le boîtier (directement sur les goujons insérés dans les parois)
- soit par l’intermédiaire de connecteurs fixés à ces mêmes goujons.
Remarque : L’utilisation de goujons à la place de trous/vis classiques n’est imposé que par des considérations esthétiques (invisibilité depuis l’extérieur du boîtier).
Le présent article présente donc les évolutions du projet ainsi que l’intégration 3D de différents constituants au travers d’un projet « multi-cartes ».
2. Modifications par rapport à la version initiale
2.1. Fonctionnalités
Les fonctionnalités proposées sont pratiquement inchangées. En dehors de la décomposition des fonctions sur plusieurs cartes, le changement majeur porte sur l’IHM. En effet, même si la microcontrôleur reste le même, la nouvelle version repose sur une interface tactile associée à un écran OLED de 1,3 pouces distribué sur le site buydisplay.com.
2.2. Modifications de l’IHM et impact sur le PCB
Les spécificités de cette nouvelle version pour la partie « contrôle » portent sur une contrainte majeure de placement des composants : s’agissant d’une carte supportant une interface tactile directement plaquée sur la face avant, aucun composant n’est présent sur cette face entièrement dédiée aux touches. On rappelle que le microcontrôleur utilisé est un composant de la famille Cypress PSoC5. S’il peut gérer directement des interfaces tactiles, la solution retenue ici a consisté à utiliser un circuit dédié (CY8CMBR3116 – cf. figure 1) permettant en outre l’ajout d’un buzzer et le contrôle de LEDs.
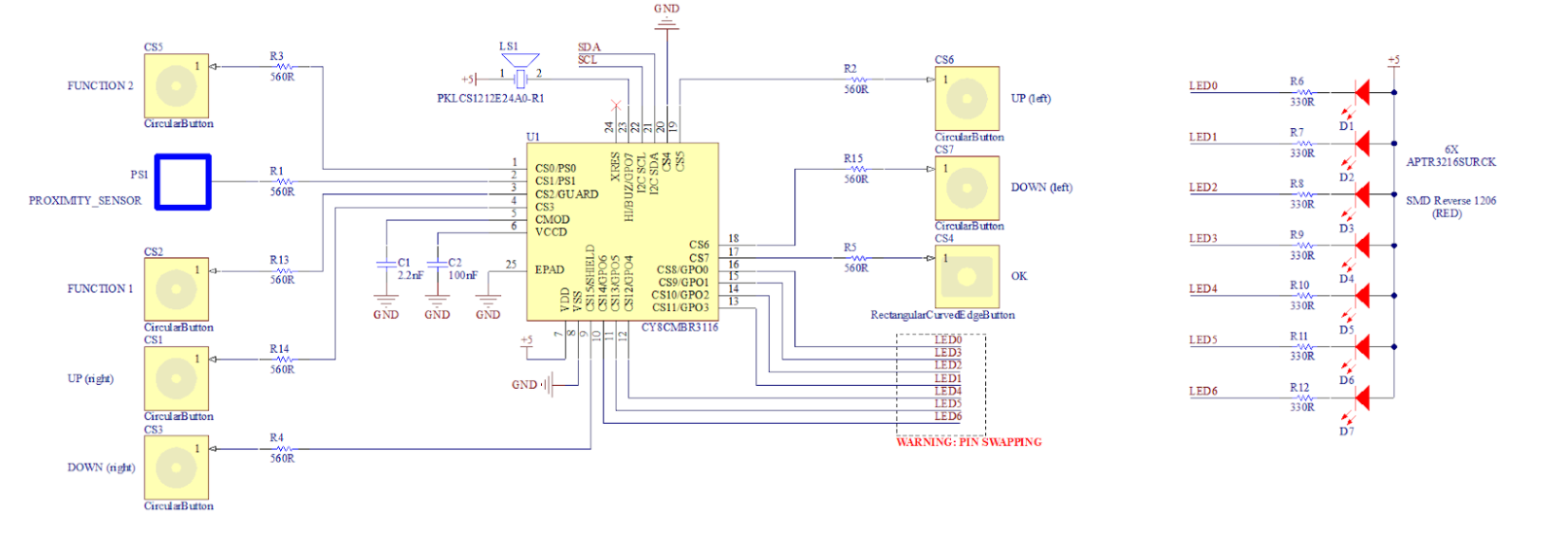
Remarque : On peut noter la présence sur ce schéma de composants particuliers (CircularButton, RectangularCurveEdgeButton) disponibles dans une bibliothèque nommée Cypress CapSense disponible sous Altium Designer. Elle permet de créer touches capacitives dédiées aux composants Cypress (autres bibliothèques disponibles : Atmel QTouch et Microchip mTouch). Les composants utilisés ici sont de simples boutons mais d’autres configurations (sliders) plus complexes sont également disponibles pour lier un symbole générique à une empreinte qui doit, la plupart du temps, être adaptée à l’application. Pour cela, une fois sélectionné sur le schéma, le menu contextuel (clic droit) donne accès à une commande « Configure … » permettant de décrire géométriquement l’empreinte associée dans le « Layout » comme illustré à la figure 2.
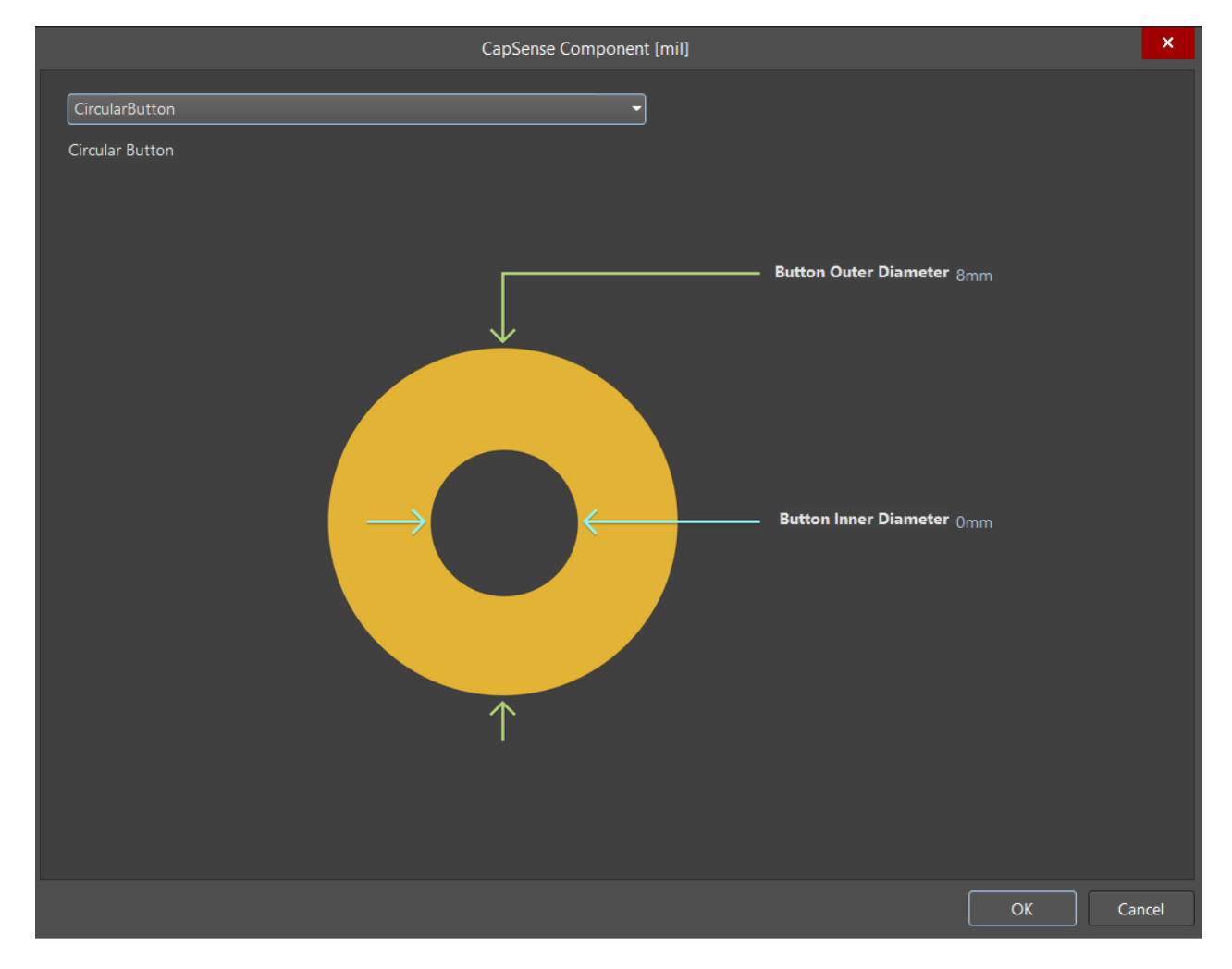
Le principe étant basé sur une variation de la capacité entre deux « électrodes » lorsque le doigt de l’utilisateur vient à proximité du PCB, certaines restrictions s’imposent sur les plans de masse et tout particulièrement pour une carte multi-couches car le diélectrique est plus fin que sur une carte double face classique. Pour pallier ce problème (de perte de sensibilité), il est recommandé dans la documentation Cypress (ici) de réaliser les plans de masse sous forme de grille (non pleins comme habituellement). Les paramètres de remplissage et de largeur des mailles de cette grilles sont clairement indiqués et doivent tout particulièrement être suivis pour un PCB à 4 couches. Des liens vers les documentations des différentes familles de circuits sont fournies à la fin de ce document pour de plus amples détails sur les règles de routage à suivre.
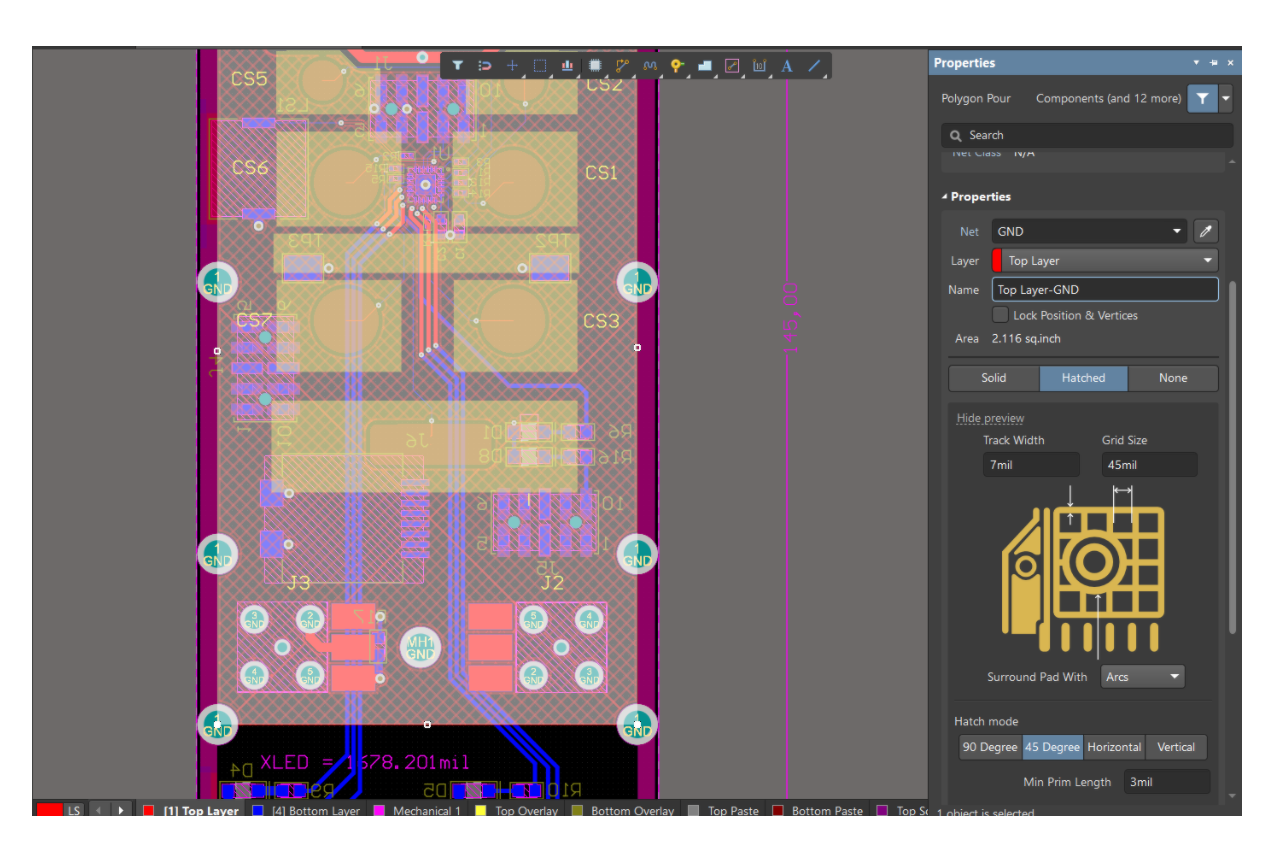
Au niveau d’Altium Designer, le paramétrage d’un plan de masse (Polygon Pour) se fait comme à l’accoutumée dans l’onglet Properties après sélection dudit plan de masse. Comme on peut le voir à la figure 3, on peut choisir la finesse de la grille ainsi que l’espacement entre les mailles de même que leur orientation. Bien sûr, une modification des paramètres impose ensuite un “rafraîchissement” (Polygon Actions > Repour Selected ou autre).
3. Projet multi-cartes et Intégration mécanique
Nous avons déjà vu dans le précédent article l’intérêt d’Altium Designer pour l’intégration mécanique d’un (ou plusieurs PCB) dans un boîtier afin de détecter d’éventuelles collisions entre pièces. Si tout ceci peut s’effectuer dans un projet classique par ajout de modèles 3D (boîtier + autres cartes), cela oblige de créer des modèles 3D desdites cartes pour les incorporer dans le projet de la carte principale voire même de les exporter dans un outil de CAO mécanique externe. Cette étape s’avère en fait inutile si l’on utilise un projet Multi-board (type disponible en bas de la liste – cf. figure 4).
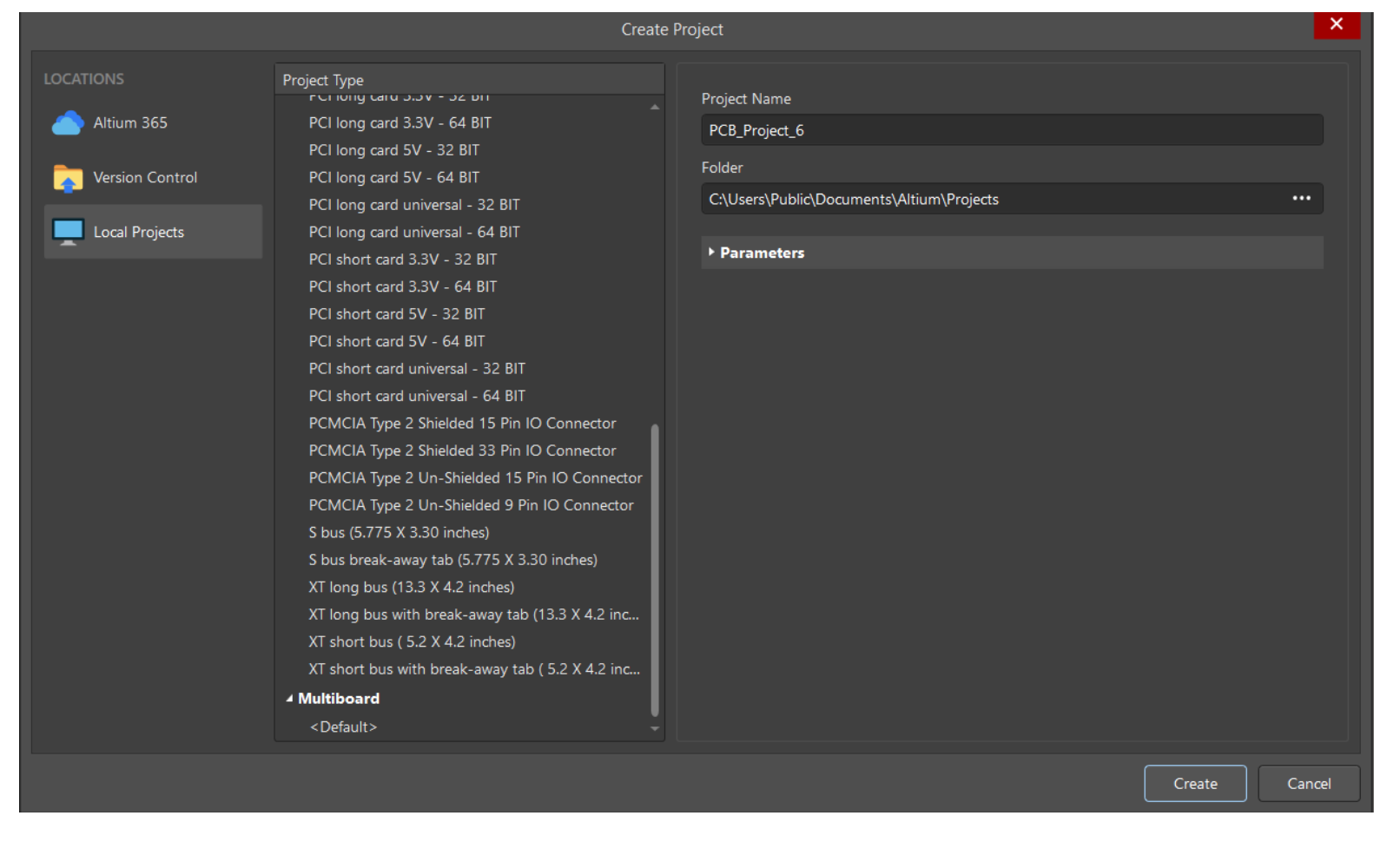
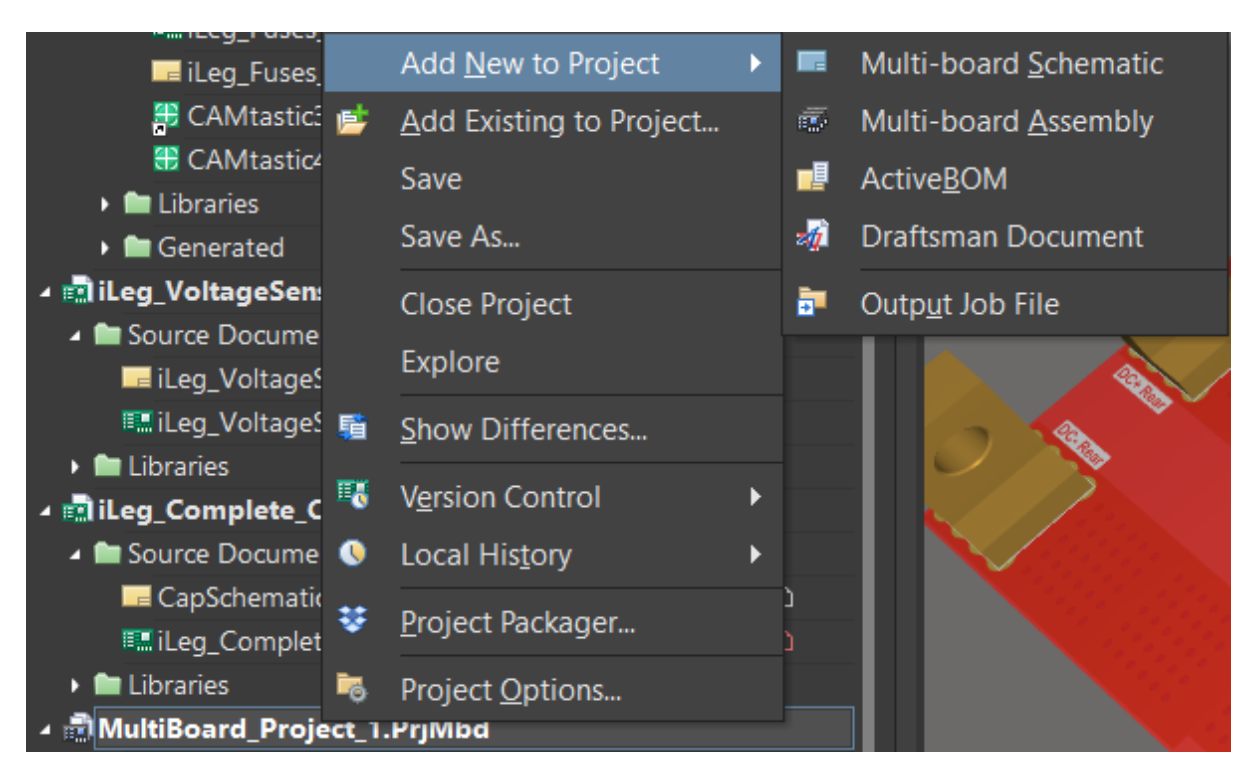
Si un tel projet permet de créer un schéma multi-cartes (cf. figure 5) et d’autres nouveaux documents, il permet aussi (et surtout dans notre cas présent), d’incorporer des « sous »-projets existants de cartes constitutives du bras de pont dans un fichier « Multi-board Assembly » (extension .MbaDoc).
A partir de ce fichier, il est possible d’ajouter (menu « Design ») :
- PCB (Insert PCB Part),
- assemblages (Insert MBA Part),
- modèles 3D au format STEP (Insert STEP Part).
L’incorporation de PCB est aisé et fournit un excellent rendu visuel comme le montre l’exemple de la figure 6.
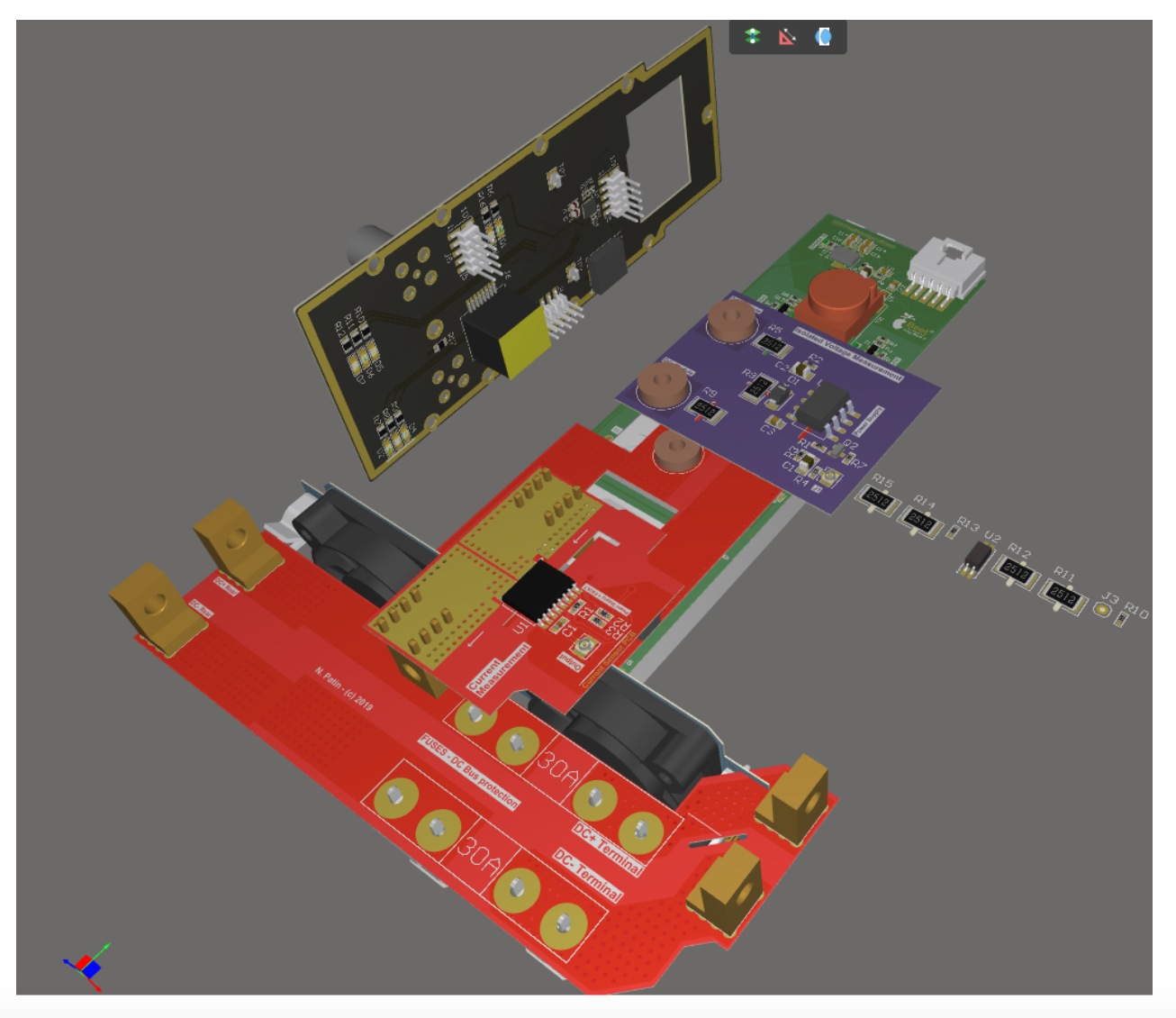
La sélection d’un PCB (ou d’un autre objet) permet alors de le déplacer à d’aide du repère local affiché à proximité (cf. figure 7). Il est en effet possible de déplacer en translation et en rotation l’objet sélectionné (avec des « accroches » tous les 90° pour les rotations suivant les 3 axes).
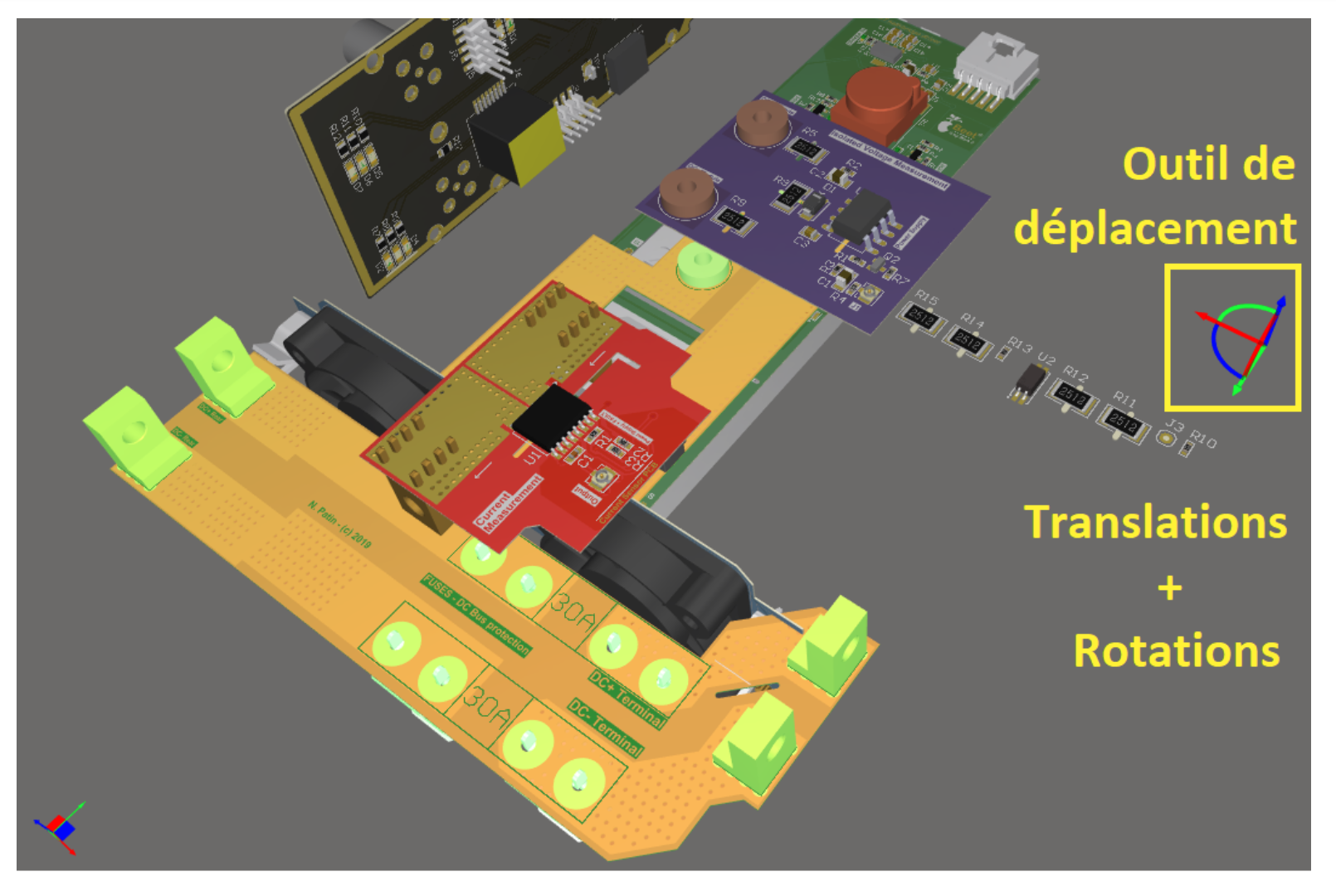
Les déplacements manuels (avec souris) peuvent s’avérer approximatifs. Pour un placement précis, on utilisera la première des trois commandes disponibles dans le bandeau de la vue « Assembly » : « Switch to Mating Mode » (ou par la commande « Shift + Ctrl + A »). Elle permet par exemple d’aligner deux trous de perçage (cf. figure 8). Pour de plus amples informations sur ce sujet, on pourra consulter la documentation d’Altium Designer ici et là. Une fois un lien (mate) établi entre deux objets, ils sont solidaires l’un de l’autre et sont déplaçables ensemble uniquement tant que ce lien n’est pas rompu (visible dans l’arborescence « Multi-board Assembly »).
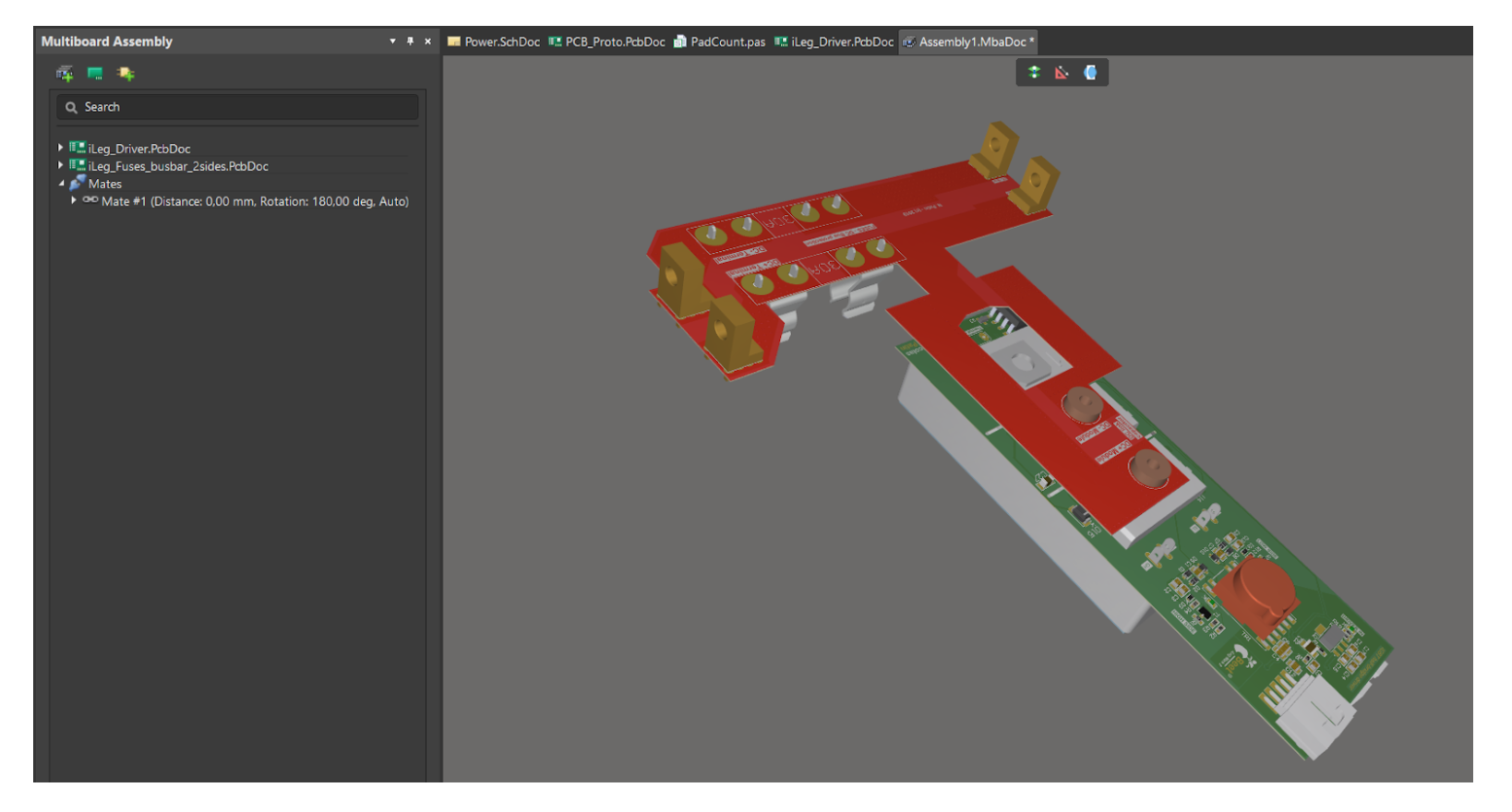
4. Conclusion
Cet article traite d’une itération d’un projet déjà présenté dans les deux articles précédents avec notamment un re-design de l’IHM utilisant une interface tactile avec ses spécificités mécaniques et électriques. En outre, il illustre la mise en œuvre d’un projet d’assemblage (Multi-board) et l’intérêt de ce type de projet pour l’intégration mécanique d’un ensemble « complexe » de cartes. L’aspect « vérification » n’a pas été abordé ici mais cet outil dispose bien évidemment de fonctionnalités de tests de collisions/violations (cf. menu Tools) et l’utilisateur intéressé pourra approfondir ce sujet dans la documentation tant pour la partie « Schéma » que pour la partie « assemblage de PCB ».