PCB Functional Testing and The Role of Manufacturer Collaboration
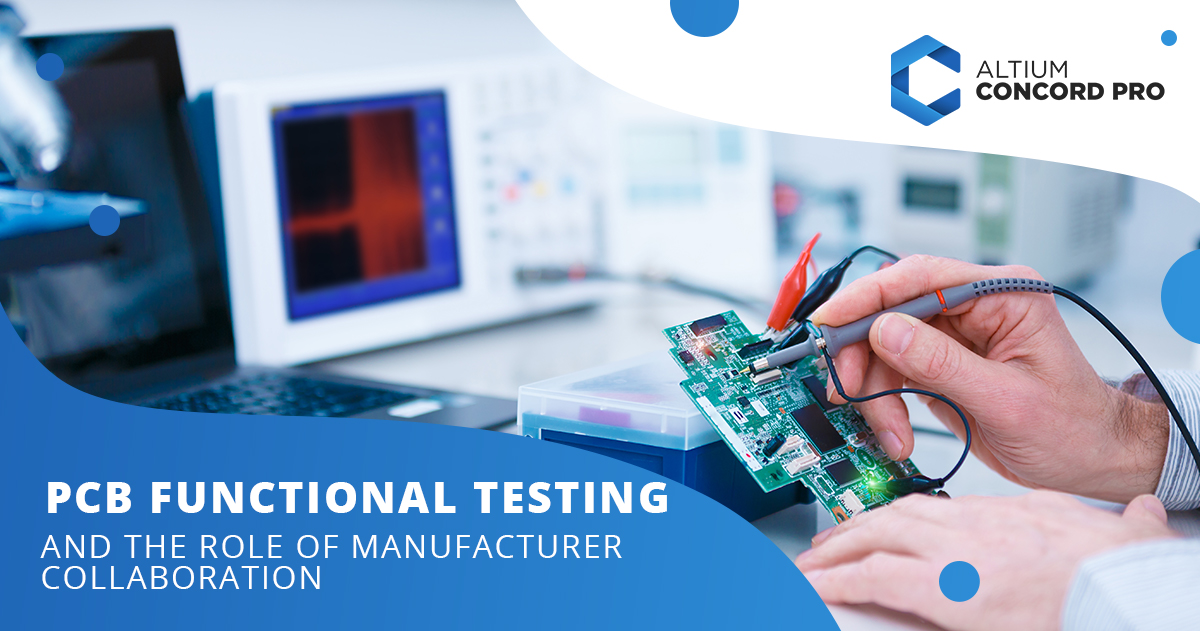
If you want to be sure your board will operate as envisioned, then it will need to pass a battery of tests during prototyping, full-scale manufacturing, and post-assembly. PCB functional testing comprises a range of tests for qualifying board functionality, encompassing everything from signal behavior to checking for short circuits. To ensure proper testing, you’ll need to make sure your manufacturer fully understands your device’s functional requirements.
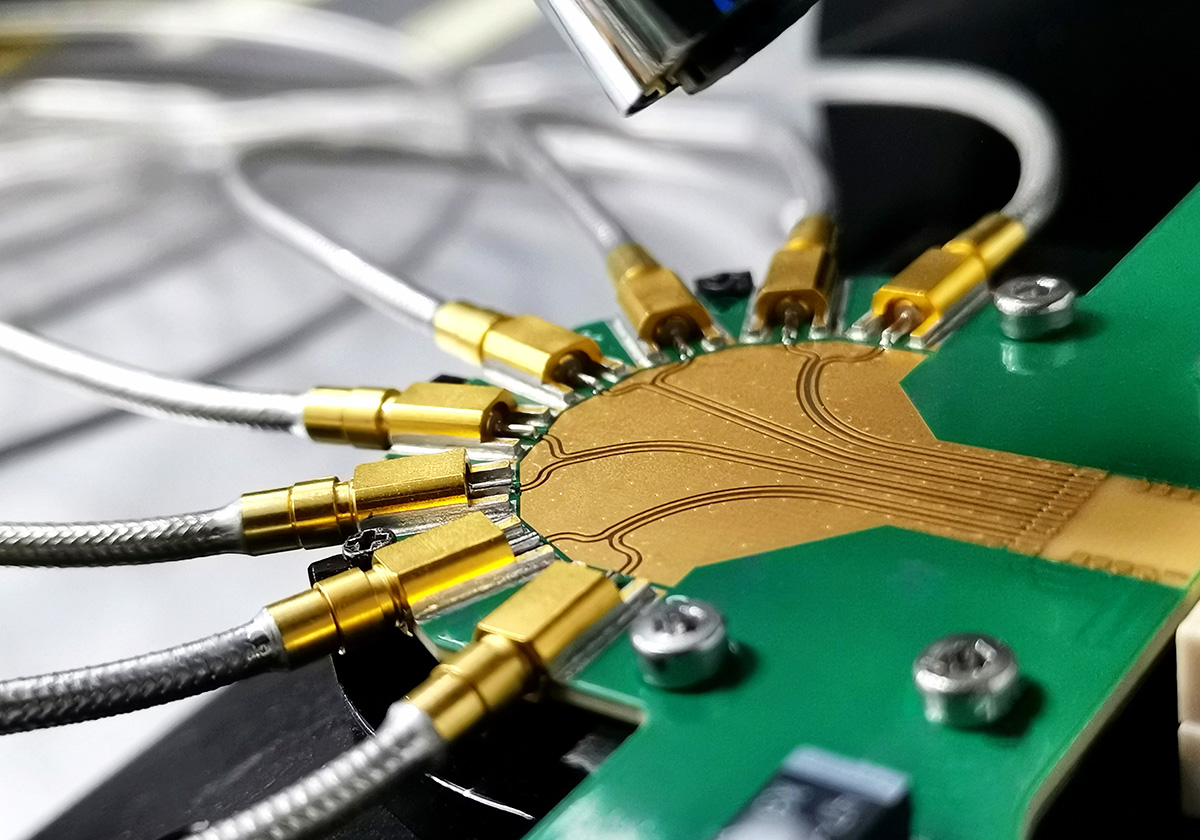
There are times where a manufacturer will need to modify your design to ensure comprehensive PCB functional testing can be performed properly. Such design modifications include adding or moving test structures, swapping or moving components, and designating in-circuit test points in your design. Rather than sending design files back-and-forth, you can speed up design qualification and ensure your manufacturer understands your testing requirements when you collaborate with your manufacturer in real time. The best way to implement this process is to use a cloud-based system for data access, sharing, and collaboration.
What is PCB Functional Testing?
Your next PCB will need to pass multiple inspections during manufacturing, including visual inspections, in-circuit tests (ICT) or flying probe tests, and even automated or semi-automated bench tests. PCB functional testing is the most comprehensive testing regimen for determining whether a manufactured board can leave the factory and be shipped to the customer. The goal is to identify manufacturing defects that affect reliability, missing or incorrect components, and opens/shorts in nets or solder connections.
Among the various sets of tests that can be performed on any board, PCB functional testing provides the most comprehensive view of signal behavior. This goes beyond in-circuit testing, where individual components are examined after being soldered in place. Functional testing provides the final go or no-go decision on a fabricated PCB. Some signal problems that can be identified in a PCB functional test are:
- Power integrity problems: excessive PDN ripple during operation, low frequency noise, and excessive jitter are some examples.
- Signal distortion and other behavior: excessive signal distortion on various nets, signal skew in buses, and other behavior in your board can be identified.
- Incorrect voltage/current: While it might sound pedestrian, incorrect voltage or current could result from placing an incorrect component, from a missing component, or from excessive IR drop somewhere in the board.
Given all the areas to be examined in a functional test, comprehensive PCB functional testing requires building a custom test fixture for your board, which can carry a hefty price tag. The costs increase when you are working with embedded software, which may require a custom test program be written. However, functional testing quickly pays for itself with high volume manufacturing runs as it helps ensure high yield and quality.
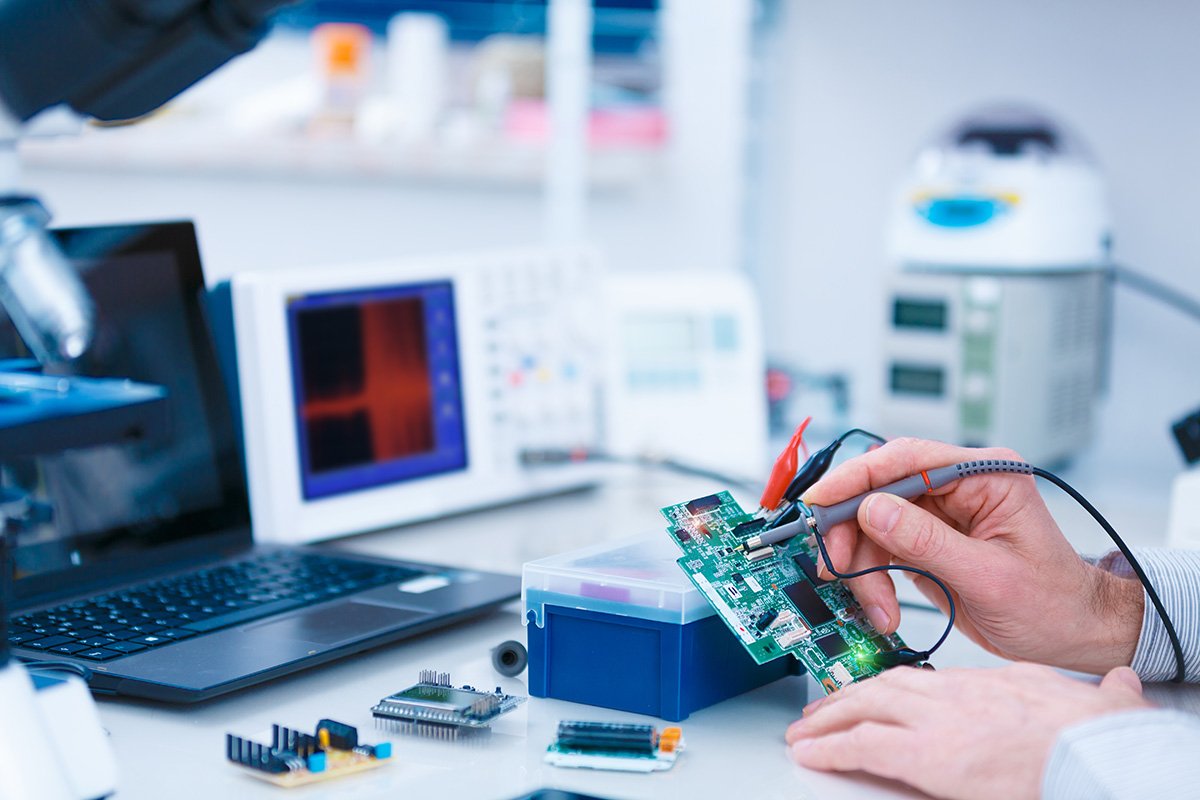
Why Manufacturer Collaboration Matters
If you’ve never designed a board for comprehensive testability, or you’re unsure of the testability of some design choices, your manufacturer can be a major asset in helping modify your design before production. Most PCB designs get put on hold before manufacturing for a variety of reasons, and some get sent back to the designers for modification. If you can collaborate with your manufacturer early in the design process, you can speed up any design modifications and reduce your turnaround time. You goal should be to ensure your board complies with your manufacturer’s DFM recommendations and testing capabilities.
To get to manufacturing quickly and ensure your board is thoroughly tested, make sure your manufacturer provides the following services:
- Qualified test engineers that continually develop functional testing hardware/software, test fixtures, and test structures.
- A suite of testing equipment for PCB functional testing, flying probe tests, ICT, and manual testing procedures as necessary.
- Visibility into the supply chain and leverage with component/laminate manufacturers, large distributors, and brokers.
- Collaboration on test development for critical circuit blocks and thorough documentation of testing results.
With the right collaboration tools that are built into your design software, your manufacturer can collaborate with you in any of these areas to ensure your PCB testing requirements are clear.
Ensure Proper PCB Functional Testing with Altium Concord Pro
When designers and manufacturers work together with a cloud-based design and data management platform, both parties will have complete visibility of all design aspects. Designers and manufacturers can easily move through the design qualification process and collaborate to ensure PCB functional testing requirements are understood and any design changes will not affect device performance. This is the type of collaborative experience you’ll find in Altium Concord Pro.
These collaboration features are accessible by both parties within Altium Designer. Each party can push proposed design changes back and forth without resorting to email, chat software, or other outdated communication methods. With advanced products that carry precise mechanical requirements, the ECAD/MCAD collaboration features in Altium Concord Pro allow real-time design collaboration on the mechanical aspects of a new product.
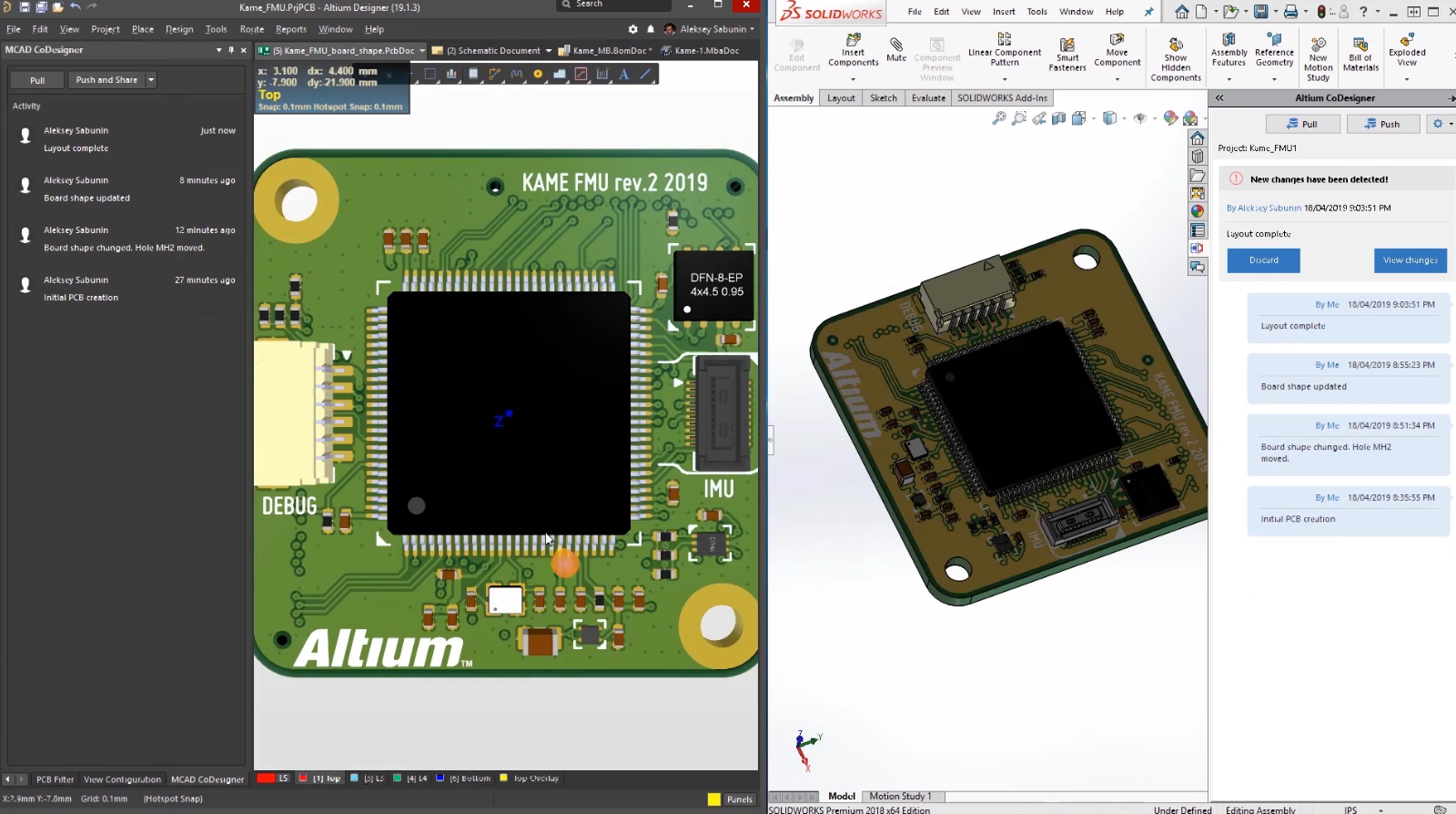
The integrated set of collaboration tools in Altium Concord Pro™ are ideal for collaborating with your manufacturer, gaining supply chain visibility, and ensuring accurate PCB functional testing during manufacturing. You’ll be able to ensure your PCB manufacturer fully understands your device’s requirements and that any design modifications do not alter device performance prior to functional testing. Best of all, these features are accessible within the industry-standard PCB design tools in Altium Designer®, forming the industry’s most powerful design and production planning platform.
Contact us or download a free trial of Altium Designer® and Altium Concord Pro™. You’ll have access to the industry’s best MCAD/ECAD co-design, PCB layout, documentation, and data management features in a single program. Talk to an Altium expert today to learn more.