Lightning Surge Protection for Electronics
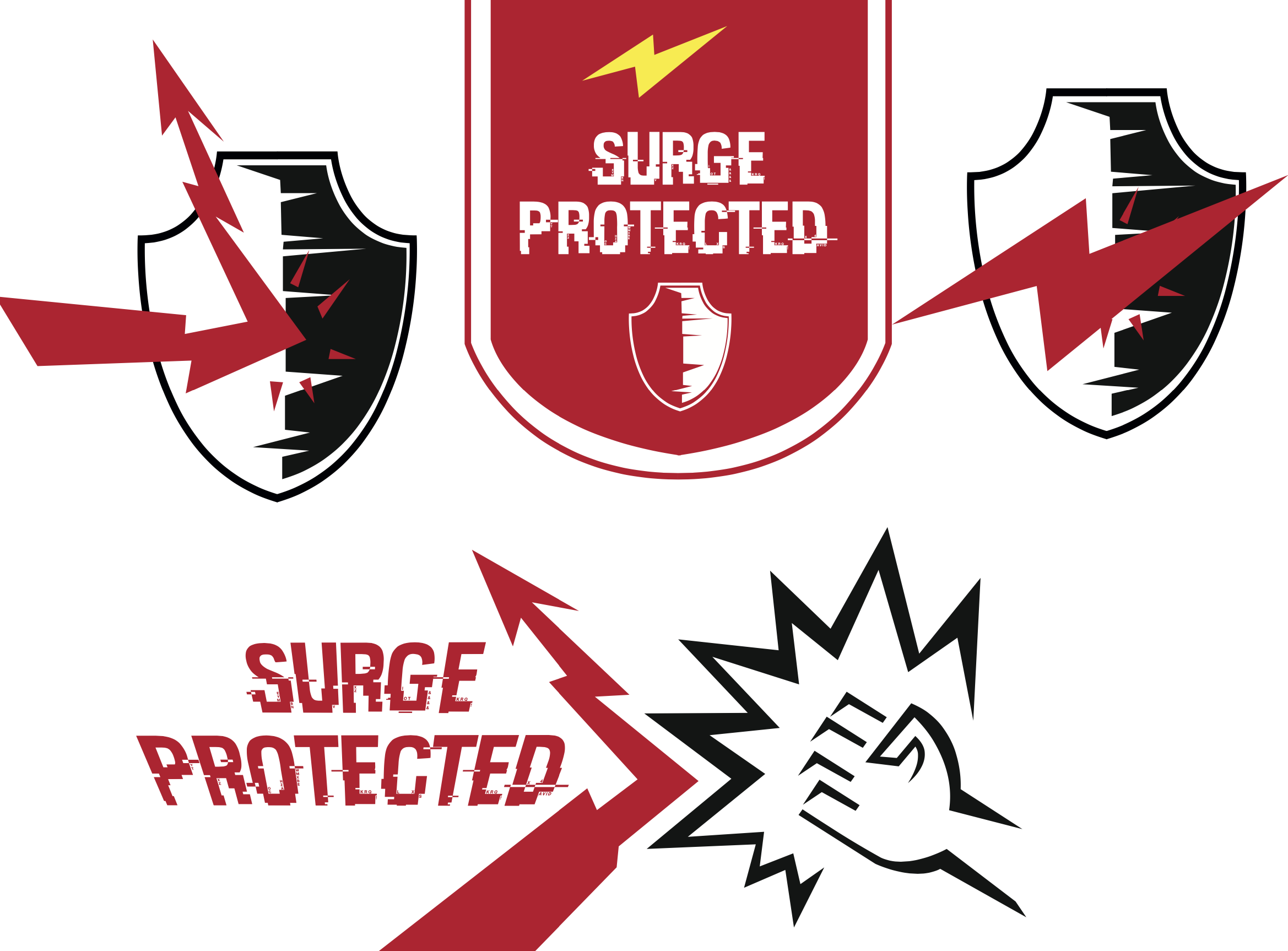
On a clear fine day, the ground typically carries a slight negative charge with a corresponding positive charge in the upper atmosphere. This generates an average electric field strength around the globe in the order of 120 V/m. By comparison, just before it discharges through a lightning strike, a thunderstorm cloud generates an electric field strength in the order of 25 kV/m. This creates a potential difference between this cloud and the ground or other charged clouds in the range of ten to one hundred million volts. A field of such intensity can cause the ionization of air molecules between the positive and negative charges, creating a conducting channel along which the lightning can travel. While most conducting channels form between clouds, at least one in ten forms between a cloud and the ground, creating a characteristic bolt of lightning.
Lightning effects
For those discharges between clouds, transitory high-intensity radio waves will be generated by the discharge. These usually are not harmful to electronic equipment unless they happen to be sensitive to such signals and in reasonable proximity to the discharge. We can discount the effect of these discharges for ground-based equipment unless transient interference from the emitted electromagnetic interference (EMI) will be a significant issue. The main problems come from those discharges that reach the earth in the vicinity of electronic devices. These lightning strikes are responsible for most of the damaging effects we experience as electrical design engineers.
Direct lightning strikes to electrical equipment and cables are generally of such magnitude that building-in protection against this event is impracticable. Lightning conductors attached to structures rely on to divert the discharge current directly to the earth as the primary protection mechanism. The probability of a direct strike on electrical equipment usually is acceptable low unless the device has been poorly or deliberately positioned. It encourages ionization in the presence of significant atmospheric electric field strengths.
Credible risks to electrical equipment come from the discharge to earth in the vicinity of the equipment. The enormous energy transfer that occurs during a lightning strike leads to the temporary generation of damaging currents in nearby electrical systems in various ways. The primary effects are typically temporary electromagnetic interference, transient voltages induced by magnetic or capacitive coupling, and surge currents caused by localized earth potential shifts. We’ll briefly summarize these three effects:
Electromagnetic interference
The flow of discharge current creates a broadband emission of EMI for the duration of the discharge. While this represents just one part of the overall electromagnetic environment for equipment, the transitory high field strength can interfere with unshielded components and transmission lines over a wide area.
Magnetic/capacitive coupling
When a discharge current passes near electrical cabling, inductive effects can cause transients to be induced onto cables. This is particularly prevalent on overhead cables carried long distances between poles or towers. It is common for electrical devices to be connected to power and signal cables that run through conducting trays, ducting, or carried via overhead cables to be affected. The longer the cables, the higher the likelihood that high voltage transients will be caused through coupling effects. This makes distantly located devices used for control and monitoring in remote locations particularly vulnerable to such events.
For a high enough magnetic or capacitive coupling level to be achieved such that it causes a significant current to be induced, the lightning current must be in very close proximity to the cabling. Such induced transient currents, however, can usually be accommodated by equipment and system design. Generally, field signal cables are screened or shielded to reduce general EMI and noise pickup. The use of twisted pair cables can reduce voltages between lines to levels that would not cause equipment damage. However, common-mode voltages can still be generated at levels that may damage sensitive components unless additional protection is added.
Earth potential shifts
Almost all lightning discharges exceed 3 kA, and around one in ten exceed 100 kA. The vast majority of earth strikes terminate directly into the ground. Those that do strike a building are usually directed to the ground via lightning conductors and ground rods. The very large discharge current flows into the ground termination and dissipates the charge into the Earth’s mass. One effect of this current is that it elevates the reference ground potential at the strike location. For example, a discharge current of 100kA terminating into the ground that has an impedance is 0.1Ω will result in a potential of 10,000 volts at the strike point. Any device close to the strike point that is grounded will be bonded to the same reference potential. While this won’t affect that device, as the potential difference it sees locally is unchanged, it will see a huge potential difference between this local ground and the ground of any cables connected to devices that are earthed some distance away. This will result in a very high transient voltage appearing due to the difference between the two ground potentials.
Lightning Impact
Transients induced onto power or signal cables due to EMI and magnetic/capacitive coupling effects are relatively straightforward to protect against. Such transients can be countered using standard shielding and screening techniques required in today’s electromagnetic emission saturated environment.
Transients induced due to potential earth shifts are a much more significant issue. Shielding will not counter possible transitory differences seen between physically separated ground levels. Low-power semiconductor components can be severely damaged by an over-voltage of just a few tens of volts. The transient voltages induced under these circumstances will require additional protection mechanisms that we will now discuss.
Protection Options
Surge protection devices can be used to protect electrical and electronic equipment from the potentially destructive effects of high-voltage transients. These devices are also known as surge arrestors, lightning barriers, and lightning protection. Surge protection circuits operate near-instantaneously to provide a low impedance path for conducting a large current to eliminate the excessive protection difference and absorb and diverting extra current to the ground to protect against the effects of transients or surges. Once the surge current has subsided, the device should ideally automatically restore regular operation and hence be able to protect against any subsequent surges. However, we’ll also briefly look at the more traditional one-shot protection devices for completeness.
Surge protection comes in two main types. Filters provide a barrier to high-frequency transient currents while allowing the low-frequency power currents to pass through unaffected. On the other hand, transient diverters provide a very low impedance path to the ground whenever the device’s voltage exceeds a preset value. Here we have focused on transient diverters as these provide the required protection from the earth potential shifts caused by a lightning strike.
Since not all circuits are likely to be exposed to these transients, an approach often taken is to use additional protective components or devices connected between general-purpose equipment, systems, and external noise or transient sources. Several components are available, which can prevent excessive energy from reaching sensitive parts of equipment or systems. These operate by diverting surges to earth or disconnecting signal lines. An acceptable device is fast in operation and capable of carrying large currents for short periods while limiting the voltage across or the current through protected equipment to levels below which damage can occur. Maintenance-free and self-resetting devices are typically preferred where interruptions to service should be avoided.
Air spark gaps
This protection mechanism consists of two conducting electrodes that are physically separated and located in an uncontrolled environment. Normally non-conducting, when the potential difference between the two electrodes reaches a defined value, then the air between them ionizes, and a discharge current flows between them. This ionization creates a low resistance path between the two electrodes, which allows a current to flow until the air ceases to be ionized. The distance between the electrodes will determine the value of the potential difference at which ionization occurs. This is effectively creating a controlled lightning strike to the local earth point.
While spark gaps are inexpensive, the voltage at which they operate will be influenced by environmental conditions such as temperature and humidity and will be affected by airborne contaminants. Their performance can also change over time and be degraded by their operation due to electrode erosion and may require replacement if they are regularly activated.
Gas discharge tubes
A variation on the spark gap protection, the conducting electrodes are physically separated in a controlled environment, typically a sealed container filled with a specific gas. This allows improved control of the discharge voltage and reduces the influence of environmental conditions. Common materials used include a low-pressure argon/hydrogen mix sealed within a ceramic container with breakdown voltages starting at 90 V and current ratings in excess of 5kA.
One disadvantage of the gas discharge tube is the finite time required for the gas to ionize, limiting protection against surge currents that have a steep rising edge to the surge waveform. A typical tube rated at 100V dc breakdown dealing with a surge with a 200V/µs rise-time will not break down until the voltage is around 200V based on an ionization time of 0.5µs. This doesn’t take into account any tolerance on the 100V rating; typically, such devices have a 20% tolerance. Another disadvantage is they are life-limited due to changes in gas pressure and composition over time.
Once breakdown has occurred and the gas has ionized, if sufficient current flows over a sustained period, the gas may convert to an ionized plasma. This plasma can discharge thousands of amps with a relatively small potential difference if the circuit can support such high current flow. The protection circuit must be designed carefully to prevent the gas discharge tube’s operation from being sustained after the source surge current has dissipated by the device’s power supply.
Gas discharge tubes are typically suited to use with low-power circuits where any surges will have slow-rising voltage conditions and can tolerate voltage overshoot conditions.
Semiconductor Devices
The advantage of semiconductor devices is their fast operation and the broad range of voltages at which they operate. As long a current flow is maintained within specification, they offer an accurate and repeatable voltage-clamp function. Surge suppression diodes, also known as transient voltage suppression (TVS) diodes, can handle several kW surges for pulses lasting less than 1 ms. The difference between a surge suppression diode and a standard Zener diode is simply down to the junction area’s increased size, reducing current density. These components offer some of the fastest response times of the available protective components (typically a few nanoseconds) but at the cost of a relatively low energy-absorbing capability. One downside of surge suppression diodes is their relatively high cost. Another is their significant capacitance that will affect circuit operation, meaning they may not simply be included as a bolt-on protective device but may have to be designed as part of the device’s development process.
Varistors
Varistors are voltage-dependent resistors where the change in current flow through the device against the voltage across the device has a non-linear relationship. As varistors are typically manufactured using metal oxide, they are generally known as metal-oxide varistors (MOVs). The metal oxide particles act similarly to a semiconductor junction. This gives them a comparable response time to surges as for a diode-based component. Their advantage over surge suppression diodes is that power is dissipated across the entire device and not just the junction area. However, the disadvantage is that they have a much higher leakage current at low voltages. They are also more significantly affected by environmental factors such as temperature and may degrade over time, particularly if regularly exposed to high current transients.
Surge relays
Surge relays are designed to disconnect the signal lines in the event of high current surges and can handle relatively high power levels. They rely on the physical movement of electrical contacts to make or break a circuit. They have the advantage of being stable and sensitive, but their main disadvantage is their operating speed. The time taken for the relay contacts to move sufficiently to affect current flow can be several milliseconds. If the surge relay is configured to break a circuit under current excess conditions, the delay can be exacerbated by arcing between the contacts during the initial time they open. This increases the time between the surge current first appearing and when the current flow is finally stopped.
Once the surge current transient has passed, the surge relay will reset back into its default state. This operation can also be relatively slow, and the physical nature of the operation can make it prone to contact bounce effects seen as transitory connection/disconnection of the circuit. Depending on the nature of the circuit, this physical bounce may have a consequential electrical impact.
Surge relays also require either maintenance to keep contacts clean or replacement if the contacts are within a sealed enclosure. Repeated operation of the contacts can lead to excessive wear due to metal erosion effects due to any arcing and impact damage.
Fuses
As a one-shot protection device, anti-surge fuses provide effective protection and use a spring tension mechanism to achieve a fast activation time. However, they can be prone to voltage overshoot issues if the transient surge current has a fast-rising edge. They rely on the surge current melting a metallic wire at a set value rather than their rating based directly on potential differences. Therefore, they must be used in combination with a resistive element to implement a protective function. Of course, the main disadvantage is the requirement for the manual replacement of the fuse after activation. It’s imperative to note that an ordinary fuse will not be capable of dealing with lightning-induced transients; a specialist surge protection fuse must be used.
Circuit breakers
Circuit breakers are generally designed for power systems. Though energy handling capability can be increased to whatever level is considered necessary, speed of response is of the order of tens of milliseconds, which is generally too slow to be effective against transients of short duration. They also require manual reset after activation making them virtually a one-shot protection device from an operational perspective. As for fuses, standard circuit breakers cannot cope with lightning-induced transients. If a circuit breaker is needed, always ensure that one correctly rated to deal with such transients is chosen.
Surge protection implementation best practice
It is common to find that one device doesn’t provide the required solution in terms of response time, current flow capability, environmental tolerance, or reliability. In that case, the answer may well be to cascade two or more different types together. This allows the designer to combine the advantages that each device offers and improve the overall protection level. The most common combination uses a high-current, relatively slow-acting component with faster acting but lower power rated component in such a way as to minimize voltage and current output. A high surge current capacity device can be used at the outer perimeter of the protection circuit to divert the bulk of the transient over-voltage, followed by a more accurate device that provides a comprehensive surge protection solution.
Surge protection devices can fulfill a range of functions depending on their implementation. They can shunt transient currents to the ground, clamp potential differences, prevent excess energy from entering a circuit or filter specific frequencies from a signal line. Usually, they fulfill a combination of these functions to achieve the required end protection. The ideal surge protection device will, as a minimum, clamp voltages, handle tremendously high surge currents, and reduce the fast-rising edge of the surge.
The protection comes from diverting surge currents to earth via a low impedance path. This path must be correctly designed and implemented if the surge protection devices’ rated performance is to be achieved. Poorly designed or implemented diversion paths can render the protection circuitry ineffective.
Protection should be applied to all external connections to the device; output signal connections are equally as susceptible as input power lines and signal connections. The most significant risk does not necessarily come from the connector with the lengthiest cable attached but from the connection that terminates with a ground connection that is physically furthest away from the ground connection of the device being protected. The same connection may not always fulfill these two criteria.
When designing surge protection or suppression into your device, consideration of cable inductance for connections is essential when calculating transient voltage protection requirements. Designs should be based on the worst-case cable options to ensure it is effective for all possible installations.
When selecting protection components, remember there is a relationship between unit price and performance. Always consider the value of the device being protected when calculating the budget for the protective elements.
The design tools in Altium Designer® contain everything you need to keep up with new technology. Talk to us today and find out how we can enhance your next PCB Design.