IPC-2551 Digital Twin Standard Released
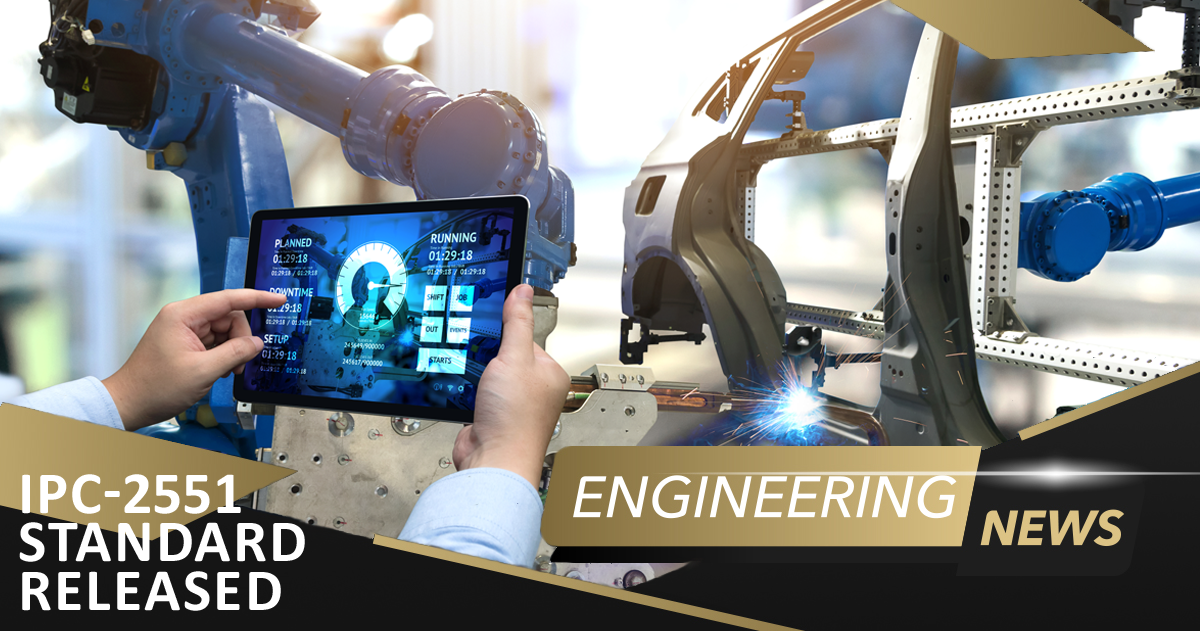
On February 8, 2021, the IPC officially released IPC-2551: International Standard for Digital Twins. This data exchange and interoperability standard has been in the works since last year before being officially released this week. IPC-2551 is the first international standard on digital twins and is targeting the creation of smart value chains with standardized data formats.
Although the IPC-2551 standard is being published by an electronics standards organization, don’t be surprised when some of its central themes and ideas appear in other digital twin standards. The idea of digital twins dates back to 2002, but it wasn’t until today’s proliferation of computing power that such a digital concept could be put to practical use.
According to IPC chief technologist Matt Kelly, the goal of the IPC-2551 standard is to reduce (or possibly eliminate) physical prototyping: “[The] benefits of establishing a digital twin framework and the tools that work within the framework will ensure that the physical expectations will be met without the need for a physical prototype...IPC-2551 will help with optimization of processes reducing losses associated with manufacturing and logistics, increasing productivity, efficiency and cost performance.”
What is a Digital Twin?
Before jumping into the meat of the new IPC-2551 standard, it helps to understand, what is a digital twin? In short, a digital twin is a digital representation of a physical object or system represented across its life-cycle. A digital twin is more than just a CAD file or 3D model of your design, it is a simulation of a real object that incorporates data gathered from the physical twin in real time. The digital twin simulation of such a physical object can be used to represent a new product as it’s being designed, manufactured, and during its operation.
If this sounds esoteric, just think of a digital twin as a virtual object that exists alongside a real object and operates in a virtual environment. The more design data that is available to create a digital twin, the more accurate the digital twin will be. Data exchange between the product and twin also flows in the other direction, enabling manufacturing digital twins to be used in perfecting a design, or allowing manufacturing to be simulated before production.
Product, Manufacturing, and Lifecycle in IPC-2551 Digital Twins
IPC-2551 digital twins are defined at three different levels:
- Product definition: The digital twin represents a single product design instance or a range of closely related product variants products, including components, ECO histories, environmental data, electrical data, and much more.
- Manufacturing information: The processes and data required to manufacture the design at scale are encoded in the digital twin, comprising everything from standard fab/assembly documentation to specific processing steps.
- Lifecycle information: The product’s lifecycle from production to recycling can be encoded in the digital twin, including details like packaging, shipping, and end-use application.
For PCB designers, this all means there will be new ways to communicate their design intent, manufacturing requirements, and other supply chain data to manufacturers, but with the added benefit provided by mass standardization. The two typical use cases for electronics digital twins include:
- Design exploration, spanning electrical, mechanical, and any other behavior
- Simulating processing and yield using digital twins of a manufacturer’s production assets and processes
These broad use cases for PCB designers rely on other universal data exchange standards from IPC.
Part of a Larger Standards Ecosystem
Some might say the IPC is stepping out of its historically core area of ensuring manufacturer quality and design reliability, but the new IPC-2551 standard keeps with the current trend of integration among different parts of the electronics value chain. This is already happening outside the electronics industry. It’s also forward looking as it pertains to data exchange between different actors within the industry. Finally, it builds on recent standards around data exchange, each of which affects a different segment of the electronics industry.
The three other relevant IPC standards that form the basis of the new IPC-2551 standard are shown in the table below. If we start reading through these standards together, we can start to see an opportunity for integration among these data exchange frameworks.
|
|
|
|
|
|
|
|
Ultimately, the new IPC-2551 defines an interoperable framework in which thousands of applications from multiple sources can work together, providing an opportunity for CAD tools and manufacturers to implement virtual prototyping, even on the factory floor. It relies on the standards listed above to capture critical design data, production data, and supply chain data in order to create digital twins of a product.
Innovative EDA software vendors like Altium will be here to help create the ecosystem around digital twins by providing design tools, architecture, and manufacturing support for electronics designers. As more clarity develops around the IPC-2551 standard and we start to see commercialized solutions, expect to see these implemented in Altium Designer® and the Altium 365® platform.