Une check-list pour accélérer le développement de vos PCB
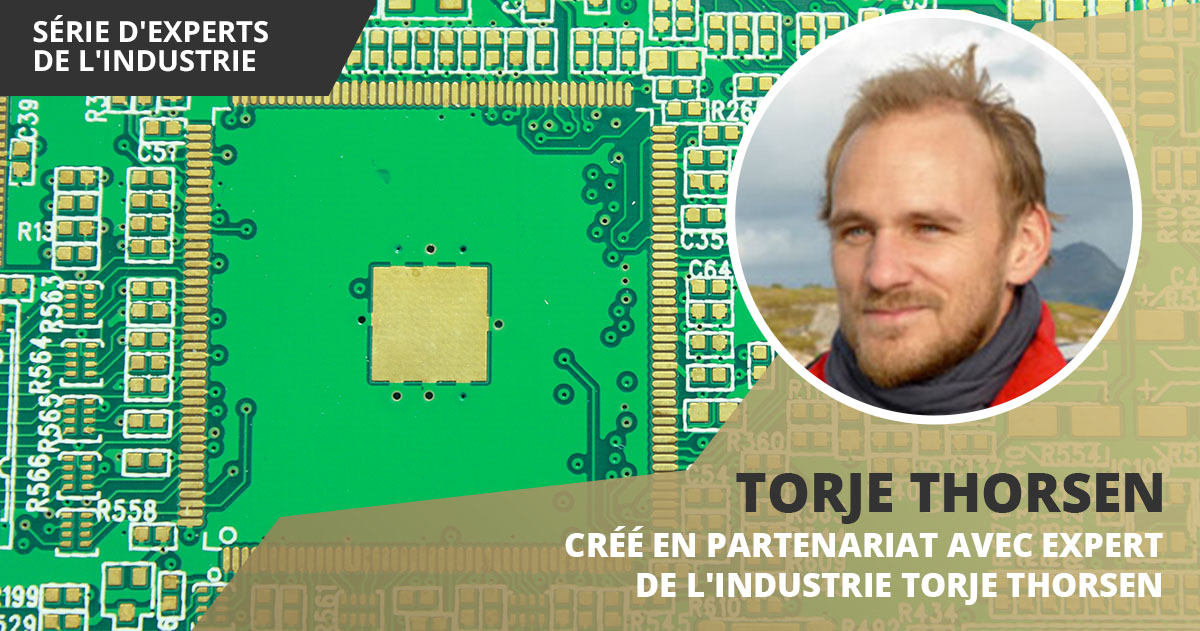
Encore de la paperasse ! Pourquoi s’embêter avec une énième procédure au lieu de se mettre au travail ?
Avec l’expérience, on a parfois tendance à faire des choix par habitude et de manière automatique, sans réfléchir. Si on a souvent raison, on risque aussi d’aller trop vite. Des petites erreurs peuvent avoir des conséquences importantes.
On utilise des check-lists dans des domaines qui requièrent une grande attention : l’aviation pour préparer le décollage d’un avion, la santé avant une intervention chirurgicale ou la sécurité comme la vérification du matériel chez les pompiers. Ces listes nécessitent de s’arrêter un instant pour vérifier méthodiquement certains points cruciaux et éviter des oublis aux conséquences graves.
Ce même principe prend tout son sens dans la CAO de circuits imprimés, où une petite coquille de conception peut avoir un impact majeur sur la production. Plus la série est grande, plus les conséquences seront importantes. Aussi, une erreur décelée trop tard dans le cycle de développement impacte les coûts de rectification (qui seront bien plus élevés). D’où l’intérêt de faire les bons choix, le plus tôt possible !
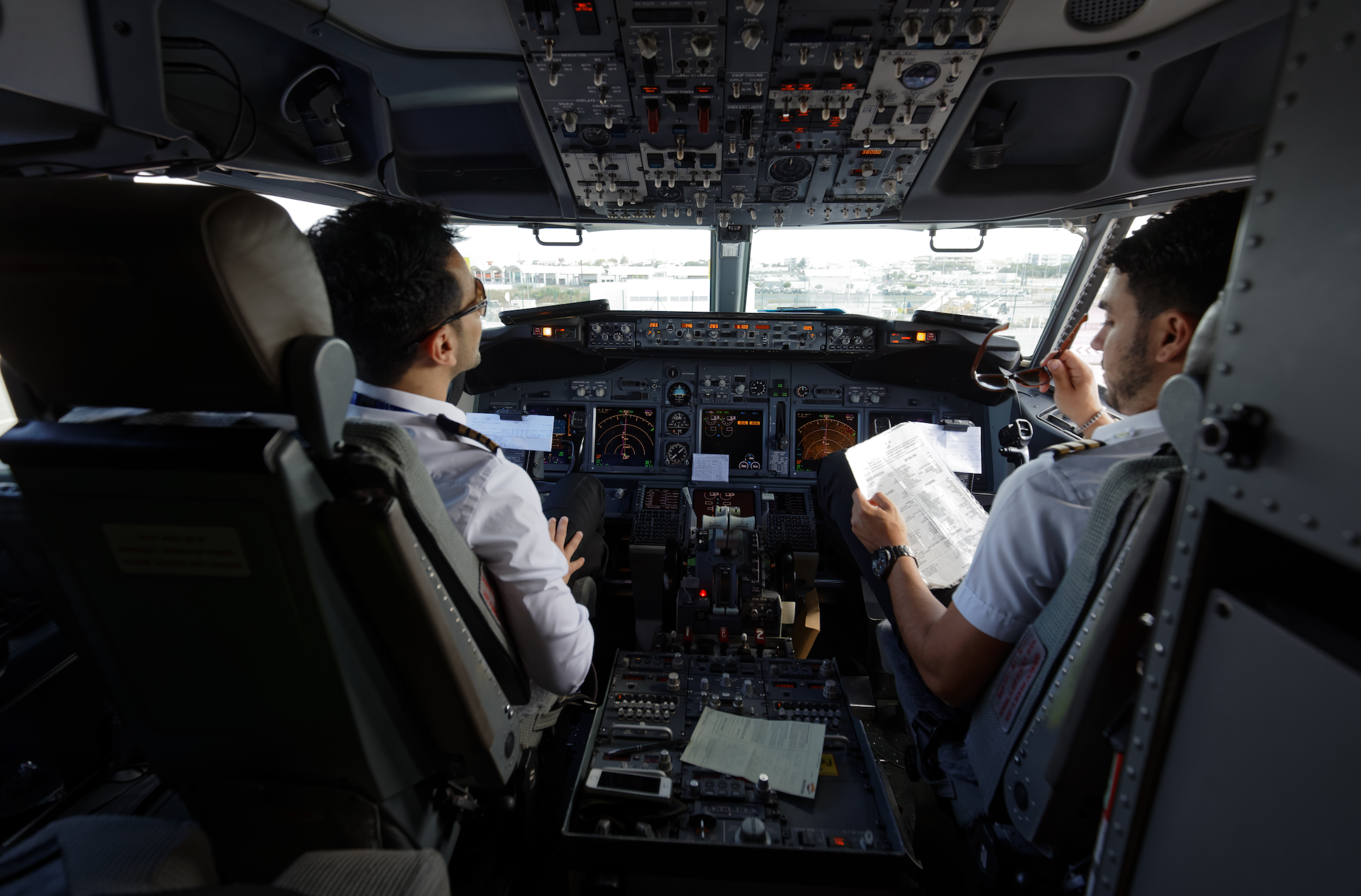
Dans cet article, je vais détailler différents points que peut contenir une check-list dédiée à la conception de circuits imprimés, à chaque étape de son avancement. À la fin de l’article, vous trouverez un lien pour télécharger un exemple non exhaustif de ce type de check-list. Bien entendu, celle-ci doit être adaptée en fonction du contexte, de votre expérience, de la nature du circuit et des contraintes propres à votre domaine.
Avant de détailler chacune des quatre sections, je vous donne déjà un avant-goût d’un thème récurrent : penser système - penser fabrication !
Section 1 : vérifications après saisie du schéma/avant lay-out
Les points de vérification dans cette section servent à s’assurer que le travail de lay-out commence sur une bonne base. À ce stade, il est relativement peu contraignant d’effectuer des modifications. Il convient de profiter de cette phase pour limiter au maximum les remises en cause ultérieures dans la séquence de travail. Voici quelques exemples de points à vérifier une fois le schéma finalisé :
- Les composants choisis sont-ils disponibles en quantité suffisante et prévus dans les délais ? Il est souvent judicieux de planifier l’approvisionnement des composants critiques avant de finaliser le circuit imprimé pour anticiper d’éventuels retards.
- Les différents bus et signaux sont-ils affectés aux bons ports et connecteurs ? Ce point concerne aussi bien l’interface vers le reste du système matériel que les contraintes liées au logiciel embarqué.
- Les protections du circuit nécessaires sont-elles en place ? Fusibles, diodes TVS et aspects ESD passent vite à la trappe.
- Les règles électriques ont-elles été bien définies, respectées et validées (ERC) ?
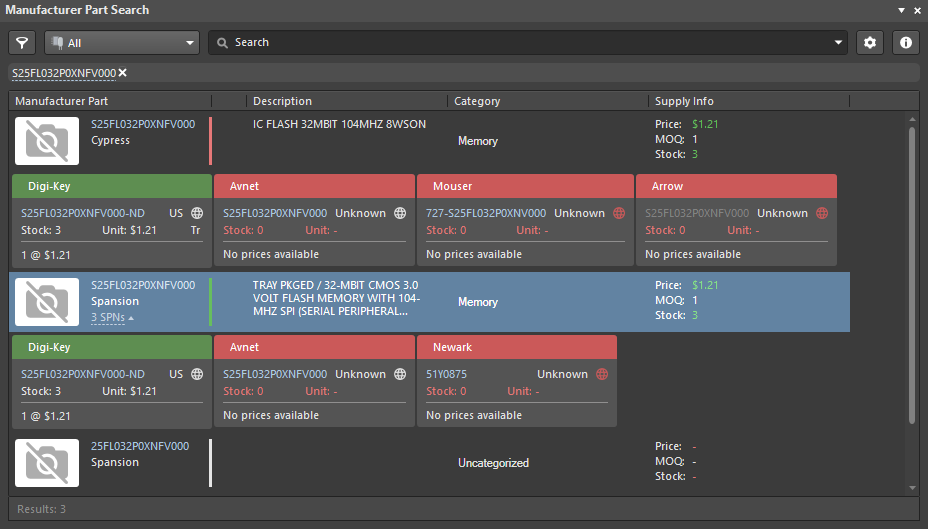
Pourtant, la toute première question à se poser avant de débuter le travail de lay-out est simple mais non anodine :
Suis-je en possession de la bonne version du schématique ?
Ce point de contrôle est particulièrement pertinent dans le cas où le schéma et le lay-out sont réalisés par des personnes ou des équipes différentes. Des échanges de mails peu structurés restent généralement le meilleur moyen de se tromper à ce niveau. Dans cette optique, Altium Designer intègre à partir de la version 18 un système de contrôle de versions basé sur les protocoles SVN et Git 1. Une fonctionnalité que je recommande fortement pour la traçabilité de vos modifications et révisions - que vous travailliez seul ou en équipe !
Pour plus d’informations sur la façon de transférer un schéma au PCB dans les règles de l’art, vous pourrez visionner la présentation « Schematic to PCB Design: Passing the Baton Like a Champion » 2, donnée par Max Seeley et Carl Schattke lors de l’évènement Altium Live 2019 à Francfort.
Section 2 : vérifications après premier placement/avant routage
Cette section sert notamment de validation de l’interface mécanique et de la connectique entre la carte et le monde extérieur. Elle permet aussi de s’assurer que l’ensemble des empreintes sont correctes et que la technologie de fabrication est bien définie. À ce stade, il convient de vérifier que votre fabricant peut traiter le stack-up choisi sans surcoût prohibitif. Le plus souvent, la meilleure approche consiste à demander les stack-up courants de votre fabricant et à définir le design en fonction des options disponibles (et non l’inverse). Penser fabrication revient à se poser quelques questions pertinentes :
- Les différentes contraintes mécaniques ont-elles été revues et validées ?
- La compatibilité avec l’interface électrique et logicielle vers le reste du système est-elle assurée ?
- La technologie de fabrication est-elle définie ? Convient-elle en termes de performances, de coût et de délai de fabrication ?
- Quelles options restent viables en matière d’assemblage ? Une carte comportant exclusivement des composants CMS sur une seule face n’est pas assemblée de la même manière qu’une carte mêlant des technologies CMS et THT sur les deux faces. Le coût n’est également pas le même !
Pour faire court, la plupart de ces points de contrôle permettent de penser au système dans son ensemble. En effet, un dispositif électronique est rarement constitué que d’un circuit imprimé et sa fabrication implique des choix qui vont au-delà de la performance électrique pure et dure.
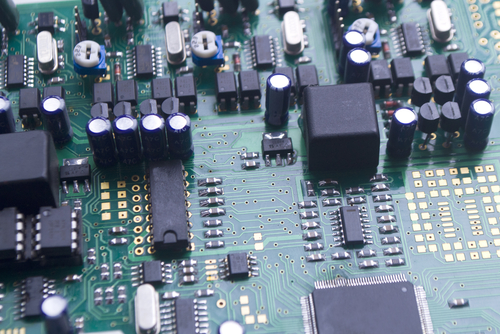
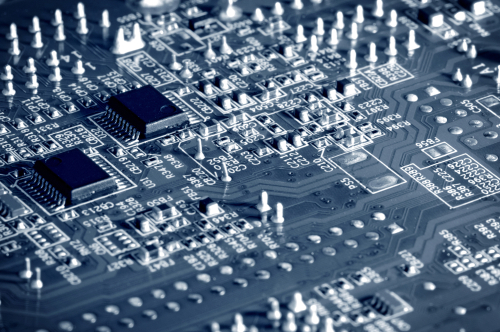

Section 3 : vérifications après routage/avant génération des fichiers de fab et d’assemblage
Il est primordial de vérifier un certain nombre d’éléments avant de se lancer dans la génération des fichiers de fabrication. Quelques exemples :
- La distribution des alimentations et le routage des signaux critiques sont-ils soignés ?
- Le DRC passe-t-il avec succès selon la classe et la technologie de fabrication définies ?
- La carte possède-t-elle les éléments « annexes » nécessaires pour la suite ? L’oubli des points de tests peut rendre le débogage pénible ou le test électrique impossible. Les mires d’alignement, l’indication de l’ordre d’empilement des couches électriques et d’autres indications utiles sont rapidement oubliées dans la précipitation.
- Les composants de puissance sont-ils bien refroidis ?
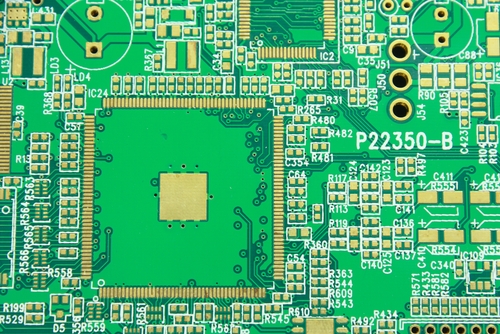
Section 4 : vérifications après génération des fichiers de fab et d’assemblage
Les derniers points à vérifier ? Les fichiers de fabrication et d’assemblage, une fois ceux-ci générés.
- Y a-t-il des artefacts non intentionnés dans les fichiers de fabrication ? L’absence d’un plan de cuivre ou le mauvais type de freins thermiques (résultant d’une fausse manipulation) sont des exemples courants d’erreurs qui peuvent être évitées grâce à un simple contrôle visuel.
- Le dossier de production est-il complet, aussi bien pour la production du circuit imprimé nu que pour son assemblage ?
- La sérigraphie est-elle bien visible et lisible pour l’ensemble des composants ?
À ce stade, il existe différentes habitudes pour la revue des fichiers. Une méthode consiste à visualiser les différents fichiers de fabrication dans un outil prévu à cet effet, couche par couche, afin de s’assurer que les données soient « propres ». Plusieurs fabricants de circuits imprimés proposent également des outils gratuits en ligne permettant de visualiser et de vérifier la cohérence de vos fichiers de fabrication.
Conclusion
Que vous soyez seul à assurer le développement complet d’un circuit imprimé du schéma aux fichiers de fabrication, ou en équipe avec de nombreux techniciens, ingénieurs et managers, les check-lists restent un outil puissant pour limiter les risques d’erreur. Elles servent notamment à :
- Prendre du recul par rapport à son propre travail afin de se poser les bonnes questions ;
- Gérer le flux d’informations entre les différents acteurs du projet, en s’assurant que les informations indispensables au bon déroulement du développement soient transmises et prises en compte ;
- Etablir et faire appliquer de bonnes pratiques au sein de l’équipe, tout en formant rapidement de nouveaux collaborateurs.
À savoir : réaliser soi-même sa propre check-list favorise l’appropriation des bonnes habitudes. À contrario, accepter une liste peu compréhensible établie par une autre personne s’avère parfois contre-productif.
L’exemple que vous pourrez télécharger ci-dessous peut sembler trop complet, ou trop simple, selon le contexte. Il sert toutefois de point de départ ou comme inspiration pour créer votre propre check-list, en fonction de vos besoins.
Check-list CAO de circuits imprimés
Bibliographie
[1] Mahpour, Ari : How to « Git » Collaborative with Altium Designer. Altium, 9 mai 2019.
Disponible sur : https://resources.altium.com/pcb-design-blog/how-to-git-collaborative-with-altium (10 mars 2020)
[2] Seeley, Max et Schattke, Carl : Schematic to PCB Design: Passing the Baton Like a Champion. AltiumLive 2019, Francfort, 23 octobre 2019. Disponible sur : https://www.altium.com/live-conference/2019/sessions/schematic-pcb-design-passing-baton-champion-0 (10 mars 2020)