Bridging the Gap Between Designers and Customers
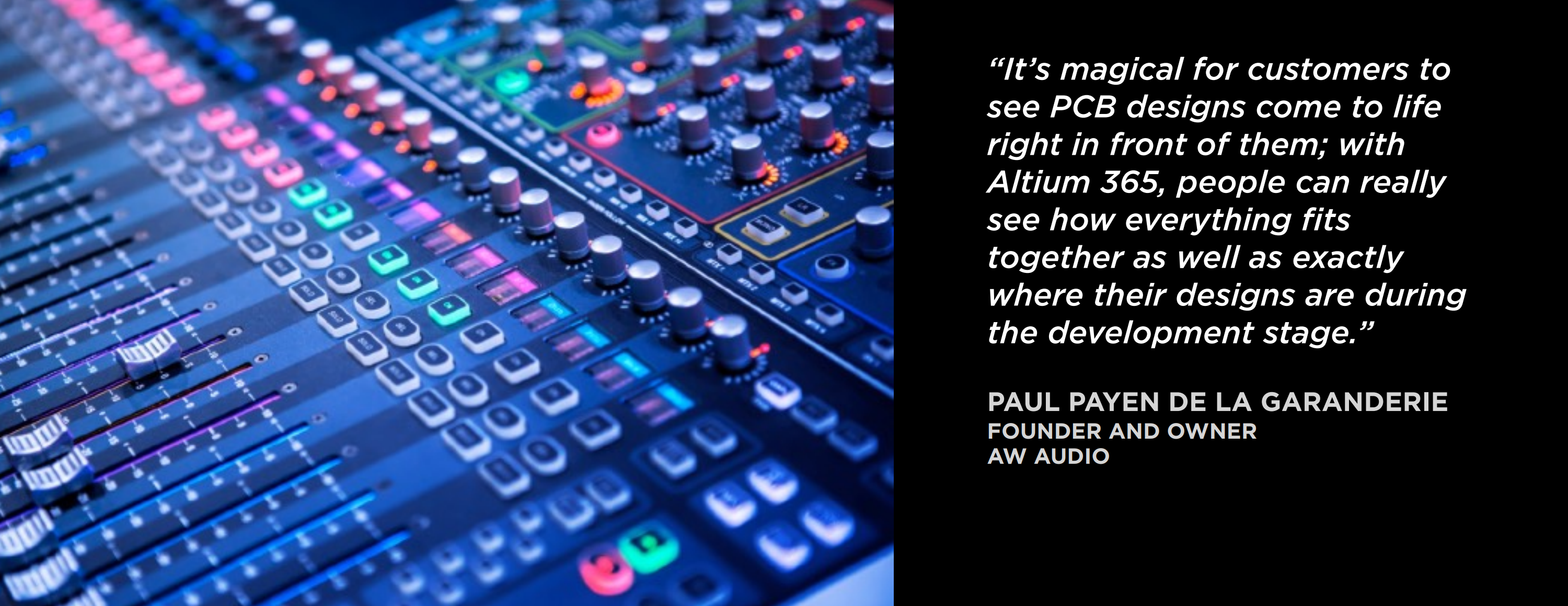
Every piece of electronic equipment starts with a great idea.
Transforming great ideas into real, physical products takes a team of talented individuals and multiple companies coming together to make everything from the internal components to the external hardware.
Printed Circuit Board (PCB) design is a specialized area of expertise that often requires outside professionals including engineering services firms. For these firms, communicating PCB designs with customers is often challenging, as visualizing the board’s development can be somewhat esoteric.
When designing electronic systems, the process can take upwards of a year and a half or more. Explaining to customers where their projects are in the pipeline can be equally challenging, as it’s difficult to share schematics and part placement during the development cycle.
Paul Payen de la Garanderie, Founder and Owner of AW Audio, an engineering services company based in France, understands these challenges very well. With an extensive background in the Audio/Visual industry, Paul has had to work with multiple companies over the years, from small start-ups to celebrated AV firms.
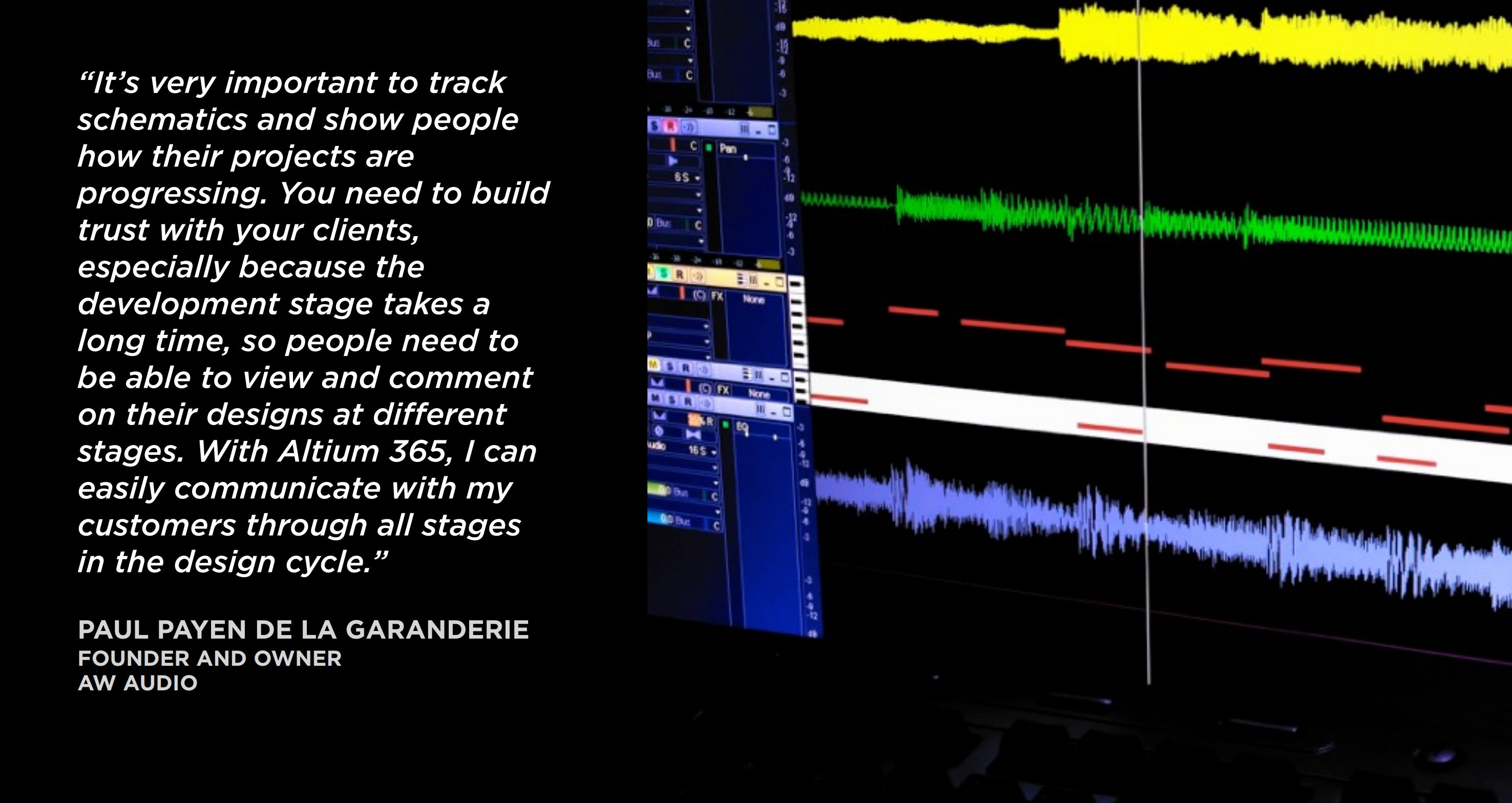
Paul is all too familiar with these challenges, from describing PCB design to showing milestones of projects in development to his customers. Hardware development is a very lengthy and costly process, which makes its customers particularly eager to see how work is progressing.
Paul made the transition to Altium Designer in part because of his manufacturing partners. ”The manufacturers wanted something they knew worked well with their workflow and what they are well familiar with—they didn’t want to work with any other PCB design format files.”
Paul soon learned that Altium software made his life easier too. Using Altium Designer®, integrated with Altium Concord Pro® enabled via the Altium 365™ cloud platform, the world’s first cloud platform for PCB design and realization, made his own processes much easier. “I was using GitHub, so it was impossible to really see how designs progressed, let alone find the parts I needed for PCB board manufacturing. I found that I could now manage board parts and libraries and easily find specific parts from various suppliers.”
With Altium Designer, Paul was able to keep his manufacturers happy, but he also needed a way to bring his customers into the loop.
As Paul explains, “It’s very important to track schematics and show people how their projects are progressing. You need to build trust with your clients, especially because the development stage takes a long time, so people need to be able to view and comment on their designs at different stages. With Altium 365, I can easily communicate with my customers through all stages in the design cycle.”
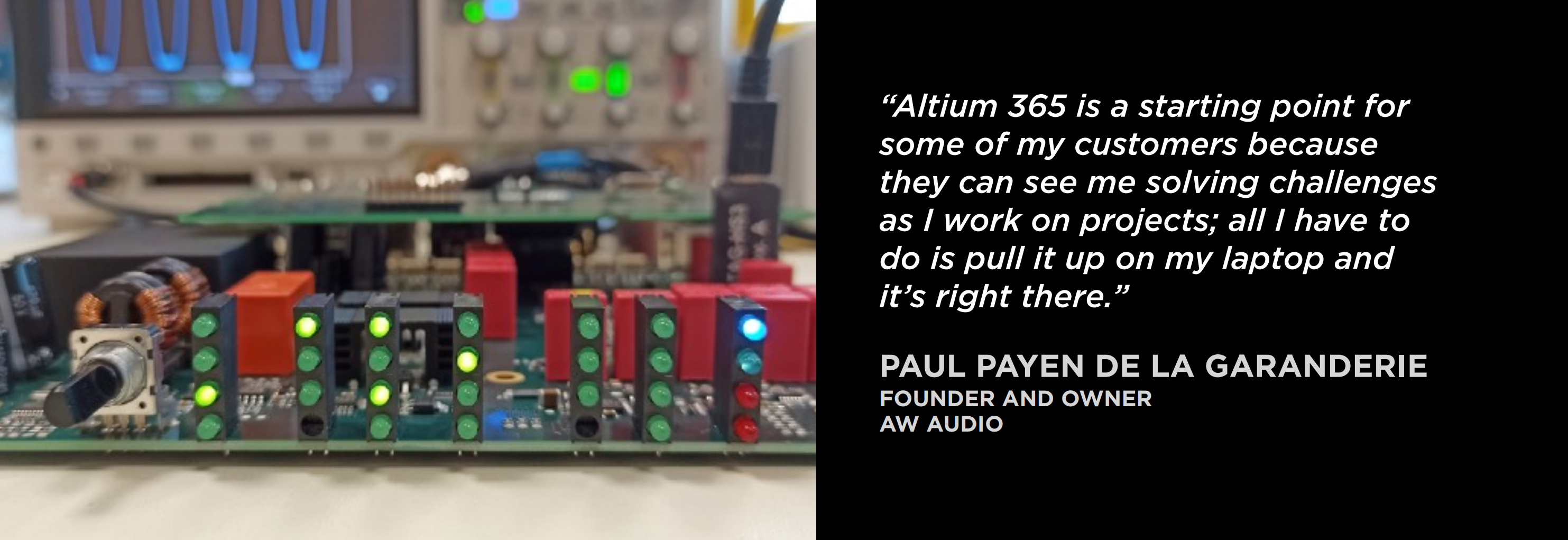
Bringing Everyone Together
AW Audio serves everyone from fledgling design houses to major AV equipment manufacturers. Some come with just ideas and others show up with schematics in hand; but they all want a way to engage in the development progress. Paul quickly found with the addition of Altium 365, he could bring everyone onto the same page, from his customers to his component manufacturers.
“It’s magical for customers to see PCB designs come to life right in front of them; with Altium 365, people can really see how everything fits together as well as exactly where their designs are during the development stage.”
Paul now uses Altium 365 every day with customers, including prospective ones. “Altium 365 is a starting point for some of my customers because they can see me solving challenges as I work on projects; all I have to do is pull it up on my laptop and it’s right there.”
As Paul moves AW Audio into more sophisticated designs and explores expanding his customer base to include universities and research facilities, Altium 365 will continue to help move him forward.
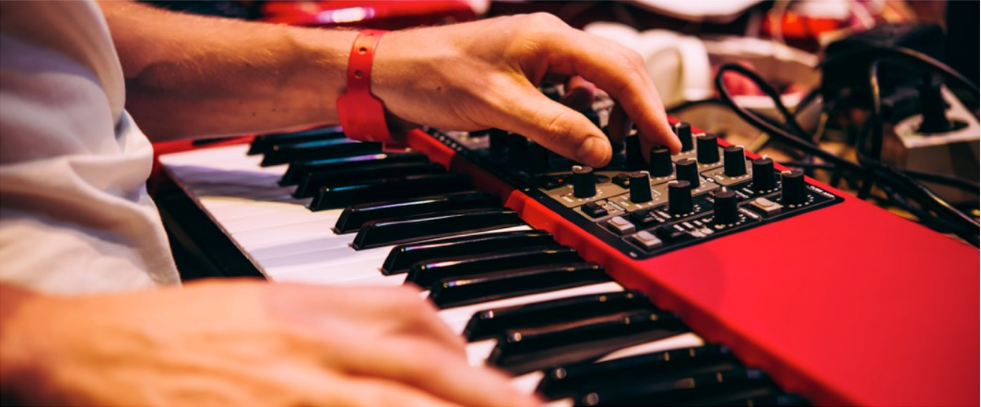