Reflexionen zum Thema Rigid-Flex – Teil 2
Wie werden Flex- und Rigid-Flex-PCBs hergestellt? In diesem Beitrag erfahren Sie, wie das fertige Produkt entsteht, indem die verschiedenen Materialkomponenten kombiniert, laminiert und zurechtgeschnitten werden.
Die Herstellung flexibler und starrflexibler PCBs
Im ersten Artikel meiner Reihe habe ich die verschiedenen Materialien vorgestellt, die bei der Fertigung dieser biegsamen Wunderwerke zum Einsatz kommen. Daran anknüpfend widme ich mich heute der Frage, wie die verschiedenen Materialkomponenten kombiniert, laminiert und zurechtgeschnitten werden. Und in meinem nächsten Beitrag gehe ich dann auf die verschiedenen Herausforderungen ein, die mit der Erstellung eines Rigid-Flex-Designs verbunden sind.
Die Zusammenfügung und Bearbeitung einer flexiblen Leiterplatte
Auf den ersten Blick erscheint der Aufbau der flexiblen Segmente eines Rigid-Flex-PCBs relativ unkompliziert. Doch da es sich um biegsame Elemente handelt, sind bei der Fertigung einige zusätzliche Schritte erforderlich. Ausgangspunkt ist dabei stets ein flexibles Trägermaterial, das einseitig oder doppelseitig mit Kupfer beschichtet werden kann. Wie ich in meinem letzten Beitrag erläutert habe, kann es sich hier um eine vorlaminierte oder unbeschichtete PI-Folie handeln, die dann mit einer Kupferschicht laminiert oder plattiert wird. Wenn das Trägermaterial mit Kupfer laminiert werden soll, muss zuvor Klebstoff aufgetragen werden. Falls die PI-Folie dagegen klebstofflos plattiert werden soll, muss zunächst eine Kupfersaatschicht aufgebracht werden. Letzteres geschieht mithilfe verschiedener Bedampfungsverfahren (beispielsweise durch das sogenannte Sputtern), die die Oberfläche für die Plattierung mit Kupfer präparieren. Am Ende entsteht so eine einseitige oder doppelseitige flexible Leiterplatte, die anschließend mit Bohrungen versehen wird. Danach werden die Bohrungen plattiert und die Leiterbahnen aufgeätzt – ganz wie bei einer konventionellen starren Leiterplatte.
Die Herstellungsschritte im Überblick
Das nachstehende animierte GIF zeigt die üblichen Schritte der Herstellung eines doppelseitigen flexiblen PCBs:
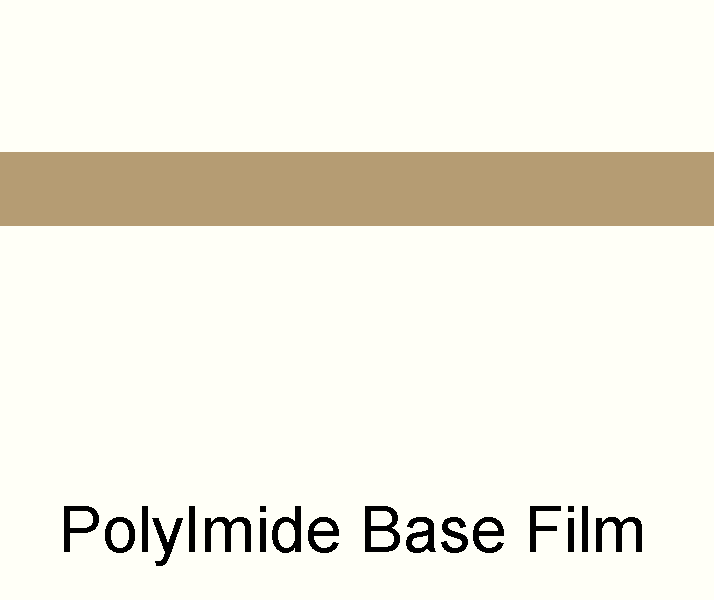
Abbildung 1: Animierte Darstellung der einzelnen Schritte der Herstellung flexibler Leiterplatten
1. Aufbringen des Klebstoffs oder Bedampfung mit einer Kupfersaatschicht (Adhesive Coating)
Wenn eine Kupferlaminierung vorgesehen ist, wird ein Epoxid- oder Acrylkleber auf das Trägermaterial aufgebracht. Alternativ kann das Trägermaterial auch durch Sputtern mit einer dünnen Kupfersaatschicht zur späteren Plattierung bedampft werden.
2. Aufbringen der Kupferfolie (Copper Foil Laminated)
Das Trägermaterial mit der Klebstoff- oder Kupfersaatschicht wird mit RA- oder ED-Kupfer laminiert bzw. plattiert.
3. Einbringen der Bohrungen (Drilling)
Die Löcher für Durchkontaktierungen und Pads werden meist mechanisch gebohrt. Dabei können plattierte flexible Substrate simultan von verschiedenen Rollen abgespult, auf demselben Maschinentisch übereinander geführt, arretiert und gebohrt und dann auf der anderen Seite wieder separat aufgespult werden. Wahlweise können die Bohrungen auch mit den von starren Leiterplatten bekannten Verfahren eingebracht werden, indem die bereits zugeschnittenen flexiblen Lagen panelisiert, übereinandergelegt, zwischen starren unbestückten Lagen fixiert und dann bearbeitet werden. Allerdings erfordert diese Methode mehr Sorgfalt und birgt den Nachteil einer geringeren Fertigungsgenauigkeit. Sehr dünne Bohrungen können nur einzeln und mithilfe von Lasern eingebracht werden, was die Fertigungskosten in die Höhe treibt. Grundsätzlich bieten Excimer- und YAG-Laser die für Microvias erforderliche Genauigkeit, während CO2-Laser zur Einbringung mittelgroßer Bohrungen mit einem Durchmesser von mindestens 4 mil (ca. 102 µm) verwendet werden. Größere Löcher und Aussparungen werden in einem separaten Fertigungsschritt ausgestanzt.
4. Plattierung der Durchkontaktierungen (Through-Hole Plating)
Die gebohrten Löcher werden mit dem gleichen chemischen Verfahren mit Kupfer plattiert, das auch bei starren Leiterplatten zum Einsatz kommt.
5. Aufbringen von Ätzresist (Etch-Resist)
Die Oberflächen der Leiterplatte erhalten einen Überzug aus lichtempfindlichem Ätzresist, das dann mit dem vorgesehenen Muster belichtet wird.
6. Ätzen und Freilegen (Etching & Stripping)
Die belichtete Kupferschicht wird geätzt. Danach wird das Ätzresist mit einem chemischen Verfahren von der Leiterplatte entfernt.
7. Aufbringen der Abdeckfolie (Coverlay)
Die Ober- und Unterseite der Leiterplatte wird mit einer Abdeckfolie überzogen, die speziell auf das spezifische PCB-Layout zugeschnitten ist. Wenn später Bauteile auf der Oberfläche des flexiblen PCBs montiert werden sollen, fungiert diese Folie zugleich als Lötstoppmaske. Meist handelt es sich dabei um eine Polyimid-Klebefolie, doch es gibt auch klebstofflose Verfahren zur Aufbringung des Coverlays. Im letzteren Fall kommt – genau wie bei der Fertigung starrer Leiterplattensegmente – ein UV-härtender Lötstopplack zum Einsatz, der auf die Oberfläche aufgetragen und dann mit dem gewünschten Muster belichtet wird. Bei der Realisierung von gröberen Designs kann der Lack auch kostensparend per Siebdruck aufgebracht werden.

Abbildung 2: Eine mit Abdeckfolie überzogene flexible Leiterplatte. Hier ist zu beachten, dass die Öffnungen in der Folie generell schmaler sind als die Pads für die Komponenten.
Üblicherweise wird die Abdeckfolie nur auf die Bereiche aufgetragen, die später tatsächlich Umwelteinflüssen ausgesetzt sind. Im Fall von Rigid-Flex-PCBs bedeutet das, dass die Bereiche ausgespart werden, die nach Abschluss der Zusammenfügung sämtlicher Lagen unter den starren PCB-Segmenten liegen – mit Ausnahme einer schmalen Überlappungszone von etwa 0,5 mm Breite. Diese selektive Beschichtung mit Abdeckfolie wird von PCB-Herstellern manchmal auch als „Bikini Coverlay“ bezeichnet (weil sie nur das Nötigste bedeckt). Zwar können Sie prinzipiell die gesamte Oberfläche der flexiblen PCB-Lagen mit einem Coverlay überziehen, doch werden dadurch der Zusammenhalt und die Z-Achsen-Stabilität der starren Leiterplattensegmente beeinträchtigt. Darüber hinaus sollten Sie darauf achten, dass die Aussparungen für Durchkontaktierungen oder Lötflächen groß genug sind und mindestens zwei Seiten des Pads als Ankerfläche freilassen. Dieses Thema werde ich in meinem nächsten Beitrag aus dieser Reihe erneut aufgreifen.
8. Zuschneiden des fertigen flexiblen PCBs
Im letzten Herstellungsschritt werden die flexiblen Leiterplattenlagen vereinzelt und auf die gewünschten Maße zugeschnitten. Bei diesem oft als „Feinschneiden“ bezeichneten Prozess wird eine Hydraulikpresse mit einem passenden Stempeleinsatz verwendet. Das hat den Vorteil, dass die Fertigung selbst relativ kostengünstig und in hoher Frequenz bzw. massenweise erfolgt, bringt jedoch zugleich hohe Werkzeugkosten mit sich. Daher wird zur Herstellung kleiner Chargen oder einzelner Prototypen ein Stanzmesser genutzt, das auf einer aus MDF, Sperrholz oder einem dicken Kunststoff wie Teflon bestehenden Trägerplatte befestigt ist und die Form der gewünschten PCB-Kontur aufweist. Bei dieser Methode werden die flexiblen Leiterplattenlagen auf die gewünschten Maße zugeschnitten, indem sie in das Stanzmesser gedrückt werden. Zur Herstellung sehr kleiner Stückzahlen ließen sich wahrscheinlich auch (ähnlich wie bei der Fertigung von Vinylschildern) Schneideplotter einsetzen.
Laminierung und Routing
Da wir uns hier vor allem für flexible PCBs interessieren, die Teil eines umfassenderen Rigid-Flex-Designs sind, schließt sich an dieser Stelle ein weiterer Schritt an: Die flexiblen Lagen müssen durch Laminierung mit den starren Segmenten verbunden werden. Dabei besteht die Besonderheit darin, dass die flexiblen Schichten viel dünner und biegsamer sind, obwohl sie in gewohnter Manier mit Bohrungen versehen, plattiert und geätzt wurden. (Wie ich bereits in meinem vorherigen Artikel erwähnt habe, könnten die flexiblen Lagen auch aus PI-Folie und Glasfasergewebe gefertigt werden, sofern die Anforderungen in puncto Verformbarkeit eher gering sind.) Daher muss jede flexible Schicht in einem starren, rahmenförmigen Panel fixiert werden, das exakt den Abmessungen der starren Panels entspricht und sich passgenau mit diesen zusammenfügen lässt.
Die Zusammenfügung der starren und flexiblen Schichten
Bei der Fertigung von Rigid-Flex-PCBs werden die Panels mit den verschiedenen starren und flexiblen Schichten durch zusätzlichen Klebstoffauftrag sowie Hitze und Druck miteinander verbunden. Sofern der Lagenaufbau verschiedene flexible Schichten umfasst, werden diese niemals direkt übereinander laminiert, damit sichergestellt ist, dass jede flexible Schicht maximal zwei Kupferlagen aufweist und dadurch die erwünschten Biegeeigenschaften behält. Zu diesem Zweck werden die flexiblen Lagen durch starre Prepreg-Segmente oder PI-Klebefolien auf Epoxid- oder Acrylbasis voneinander separiert.
Die starren Panels werden vor der Zusammenfügung in den Bereichen ausgefräst, in denen sich später die Biegebereiche der flexiblen Lagen befinden.
In den Abbildungen 3 und 4 sehen Sie die Anordnung der Lagen bei der Zusammenfügung eines Rigid-Flex-PCBs mit drei starren und zwei flexiblen Schichten.
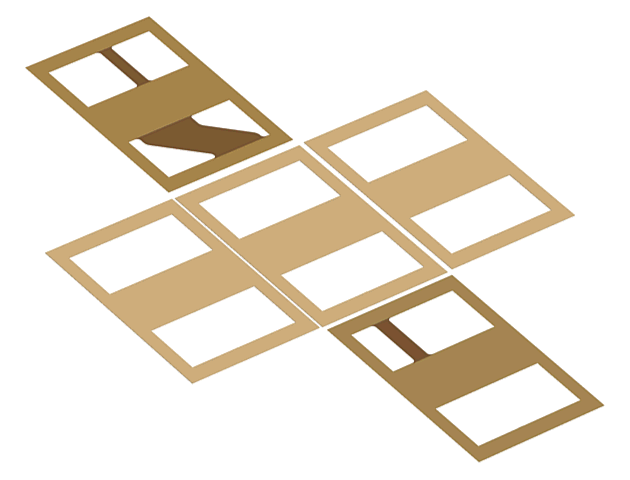
Abbildung 3: Modus der Stapelung der (geätzten, plattierten und mit einer Coverlay-Folie überzogenen) flexiblen Schichten und der starren Glasfaser-Epoxidharz-Panels
Abbildung 4: Detailliertes Diagramm des Lagenaufbaus, in dem auch die plattierten Durchkontaktierungen der flexiblen Schichten sowie die alle Lagen durchschneidenden Durchkontaktierungen in den starren Segmenten dargestellt sind.
Abbildung 4 zeigt exemplarisch den Lagenaufbau eines Rigid-Flex-Designs mit zwei flexiblen Lagen, die jeweils doppelseitig plattiert und geätzt sind. Diese flexiblen Lagen wurden nach dem Feinschneiden in starren Panelrahmen fixiert, damit sie bei der Zusammenfügung mit den starren Segmenten und der anschließenden Bestückung ihre Form behalten. Das ist nur eine von vielen Maßnahmen, die zur Vermeidung von Beschädigungen gekrümmter oder großflächig bloß liegender flexibler Segmente in der Bestückungs- und Montagephase getroffen werden können. (Im nächsten Beitrag dieser Reihe, der der Erstellung von Rigid-Flex-Designs gewidmet ist, werde ich mich ausführlicher mit dieser Thematik befassen.)
Des Weiteren wird aus Abbildung 4 ersichtlich, dass die Außenseiten der obersten und untersten starren Segmente nach der erfolgreichen Zusammenfügung sämtlicher Lagen ebenfalls mit Kupferfolie laminiert werden. Dann werden durch das Einbringen und Plattieren weiterer Bohrungen Durchkontaktierungen erzeugt, die sämtliche Lagen miteinander verbinden. (Hier können wieder die bereits erwähnten laserbasierten Verfahren zum Einsatz kommen, die einerseits kleinere Durchmesser ermöglichen, andererseits aber teurer sind.)
Der letzte Schritt vor der Bestückung und Montage umfasst das Aufbringen des Lötstopplacks und des Bestückungsdrucks auf die Außenflächen der starren Segmente. Ergänzend erfolgen Oberflächenbehandlungen wie ENIG oder HASL.
Physikalische Beschränkungen
Designs mit mehreren flexiblen Lagen
Auch wenn sich prinzipiell jeder beliebige Lagenaufbau als Rigid-Flex-Design realisieren lässt, kann dies schnell sehr teuer werden. Um unerwartete Mehrkosten zu vermeiden, sollten Sie die verschiedenen Produktionsschritte sorgfältig planen und dabei die Eigenschaften der gewählten Materialien berücksichtigen. Behalten Sie stets im Gedächtnis, dass die flexiblen Lagen mechanischen Belastungen ausgesetzt sind, wenn die Leiterplatte gebogen wird. Speziell bei zyklischer Belastung und kleinen Biegeradien neigen Kupferschichten – wie bereits im letzten Beitrag erwähnt – zu Brüchen infolge von Kaltverfestigung und Materialermüdung. Sie können diesem Problem begegnen, indem Sie für Ihre flexiblen Lagen ein Design mit einer einzelnen Kupferschicht wählen. So sorgen Sie dafür, dass die Trägerschicht dem größten Druck und die Coverlay-Folie dem größten Zug ausgesetzt ist, während die Kupferschicht um die Nulllinie zu liegen kommt (wie in Abbildung 5 dargestellt). Da die PI-Folien extrem gute elastische Eigenschaften aufweisen, erzielen Sie hier eine sehr viel höhere Lebensdauer als bei Designs mit zwei (oder mehr) Kupferlagen pro flexibler Schicht.
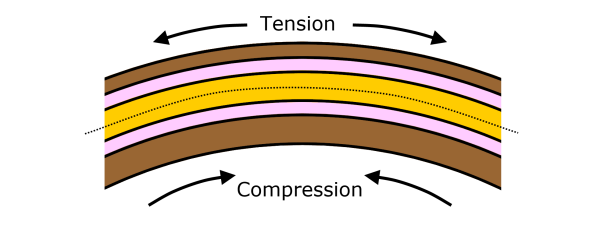
Abbildung 5: Bei zyklischer, hochfrequenter Biegebelastung sollte ein Design mit einer einzelnen Schicht aus RA-Kupfer gewählt werden. Das verlangsamt die Materialermüdung und maximiert so die Lebensdauer des PCBs.
Darüber hinaus ist es bei PCBs mit mehr als einer flexiblen Lage empfehlenswert, das Design so auszulegen, dass Knicke und Biegungen in einander überlappenden Bereichen vermieden werden, wenn der Biegeradius durch die Länge der flexiblen Segmente beschränkt wird. Doch halt! Ich greife mir selbst vor. Sparen wir uns diese Überlegungen für den nächsten Beitrag auf und kehren wir zum heutigen Thema zurück...
Klebstoffperlen
Wie ich in meinem vorherigen Artikel bereits erwähnt habe, bietet es sich in manchen Fällen an, die Übergänge zwischen starren und flexiblen Segmenten mithilfe von Epoxid-, Acryl- oder Heißkleber zu stabilisieren, um die Lebensdauer des Rigid-Flex-PCBs zu steigern. Allerdings kann das Auftragen und Härten dieser Substanzen einen beträchtlichen Mehraufwand bedeuten.
Wenn Sie sich hier für den Einsatz einer automatisierten Dosierstation entscheiden, sollten Sie unbedingt in enger Zusammenarbeit mit den Montageingenieur sicherstellen, dass beim Betrieb der Anlage kein Klebstoff auf andere Leiterplattenelemente heruntertropft. Falls dies nicht möglich ist, muss der Klebstoff manuell aufgetragen werden, was den Zeit- und Kostenaufwand zusätzlich erhöht. Grundsätzlich erfordern beide Varianten eine saubere Dokumentation Ihrer Anforderungen an den Herstellungsprozess, an der sich die Fertigungs- und Montageingenieure orientieren können.
Versteifungen und Steckverbinder
Die Leiterbahnen der flexiblen Lagen münden entweder in starre PCB-Segmente oder laufen in Steckverbindern aus. Im letzteren Fall kann der Ausgang mithilfe einer Versteifung (aus einer dicken PI-Klebefolie oder Werkstoffen der Klasse FR-4) stabilisiert werden. Da dies einen Mehraufwand bedeutet, bietet es sich an, die Ausgänge der flexiblen Leiterbahnen in die starren Segmente einzubetten.
Bestückung im Panel
Nach der Zusammenfügung der einzelnen Schichten verbleibt der Rigid-Flex-PCB zunächst in seinem Panel, damit die gewünschten Bauteile an den vorgesehenen Stellen der starren Segmente platziert und festgelötet werden können. Falls zusätzlich eine Bestückung der flexiblen Segmente vorgesehen ist, muss das Panel um zusätzliche starre Bereiche erweitert werden, die bei der Bauteilmontage für die nötige Fixierung sorgen. Diese Fixierungselemente sind nicht mit den flexiblen Segmenten verklebt, sondern durch gefräste Nuten und Perforationslinien abgetrennt. Dadurch können sie nach der Bestückung von Hand ausgebrochen werden.
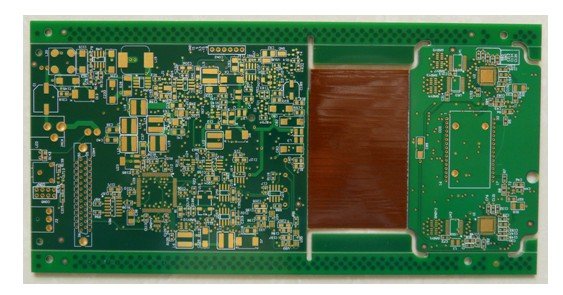
Abbildung 6: Beispiel eines Rigid-Flex-Panels mit zwei starren Segmenten, die über ein flexibles, mit Fixierungselementen versehenes Segment miteinander verbunden sind. Die starren Seitenelemente des Panels sind teils durch eine V-Nut abgetrennt, damit sie sich später leicht ausbrechen lassen. Das spart bei der Montage des fertigen PCBs im vorgesehenen Gerätegehäuse wertvolle Zeit.
Fazit
Der vorliegende Artikel ist kaum mehr als ein kursorischer Überblick über die verschiedenen Schritte der Herstellung von Rigid-Flex-PCBs, bietet Ihnen jedoch einen guten Einstieg in die Thematik. Außerdem enthält er alle nötigen Informationen, die Sie als Grundlage für den dritten Teil dieser Reihe benötigen, in dem ich mich eingehend mit vielen fertigungsrelevanten Aspekten der Erstellung von Rigid-Flex-Designs befasse.
Ich hoffe, dass Ihnen die Lektüre Spaß gemacht hat, auch wenn ich viele interessante Details unerwähnt lassen musste. Wenn Sie mögen, können Sie mir gern Kommentare und Fragen schicken und mir Ihre Erfahrungen mit Rigid-Flex-Designs mitteilen. Ich freue mich darauf, von Ihnen zu hören. :-)