Materiale Core vs. Prepreg PCB: Cosa C'è da Sapere per i Designer
I sometimes get questions from designers that want to know more about the PCB material selection and manufacturing process. Although I’m not a manufacturer, it behooves designers to understand something about the materials they have available when working on a new project. One question I get is on the exact differences between PCB core vs. prepreg materials. The terms are sometimes used interchangeably, including by novice designers; I’ll admit I’ve been guilty of this.
Once the difference between core and prepreg is clear, what exact material should you use for your application? How do the important electrical parameters change during plating, etching, and curing? As more designers must become intimately familiar with working at GHz frequencies, these points become quite important for properly sizing traces on these materials and avoiding complicated signal integrity problems.
The Difference Between PCB Core vs. Prepreg
PCB cores and laminates are similar and, in some ways, quite different. Your core is effectively one or more prepreg laminates that are pressed, hardened, and cured with heat, and the core is plated with copper foil on each side. The prepreg material is impregnated with a resin, where the resin is hardened but left uncured. Most manufacturers describe the prepreg as the glue that holds core materials together; when two cores are stacked on each side of a prepreg laminate, exposing the stack to heat causes the resin to begin bonding to the adjacent layers. The hardened resin slowly cures through crosslinking, and its resulting material properties start to approach those of the core layers.
The resin material encases a glass weave, and the manufacturing process for this glass weave is very similar to that used to manufacture yarns. The glass weave can be quite tight (e.g., 7628 prepreg) or loose (e.g., 1080 prepreg), which is controlled with a loom during manufacturing. Any gaps and the overall homogeneity of the yarn will determine the electromagnetic properties, which is then responsible for dispersion, losses, and any fiber weave effects seen by signals in the board.
FR4 PCB core/prepreg weaves and their important material properties
PCB core vs. prepreg materials can have somewhat different dielectric constants, depending on the resin content, type of resin, and glass weave. This can be a problem when designing boards that require very precise impedance matching as the effective dielectric constant seen by a signal on a track depends on the dielectric constants of the surrounding materials. Not all prepreg and core materials are compatible with each other, and core/prepreg stacks with very different dielectric constants make it difficult to predict exact dielectric constants and losses in an interconnect (see below).
With any PCB core or prepreg material, creepage and leakage current is a concern at high voltage. Electromigration of copper and subsequent growth of conductive filaments are one reason for creepage specifications for FR4 materials. This problem, as well as a desire to increase glass transition and decomposition temperatures, motivated a switch to non-dicyandiamide (non-DICY) resins in FR4 cores and laminates. Phenolic resins provide higher decomposition and glass transition temperatures compared to DICY resins while also providing higher insulation resistance after full curing.
Effective Dielectric Constant for Core and Prepreg Materials
With the obvious structural variations in core and prepreg materials, getting an accurate value for the dielectric constant and loss tangent is important from a signal integrity standpoint. When your signals have low rise time, you can probably get away with taking a value from a marketing datasheet. Once your knee frequencies or analog signals hit the GHz range, you need to be careful with values quoted from datasheets, especially when modelling interconnect behavior and using impedance controlled routing.
The problem with datasheet values is that the actual dielectric constant measured depends on the test method, routing geometry, specific frequencies (especially in the GHz range), resin content, and even material thickness. John Coonrod has discussed this problem extensively in a recent podcast. The weave pattern in PCB core/prepreg materials makes them highly inhomogeneous and anisotropic, meaning the important material properties vary in space and along different directions. This is the reason we have fiber weave effects, such as skew and fiber cavity resonances.
You might be thinking, why should the thickness of a laminate matter when characterizing material properties? The reason is that the important parameter that characterizes signal behavior is the effective dielectric constant (remember, this is a complex quantity!), which depends on the trace dimensions and layer thickness you use in you material. Take a look at these articles for microstrip and symmetric stripline transmission lines.
Finally, the other important parameter to consider is the copper roughness on a given laminate. The two articles I linked to above provide effective dielectric constant values for microstrip and stripline transmission line geometries while assuming no copper roughness. However, there is a simple linear approximation you can use to account for copper roughness:
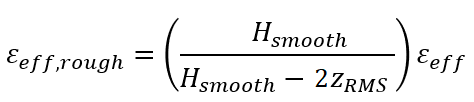
Effective dielectric constant with copper roughness
In this equation, H is the thickness of the dielectric, and zRMS is the root-mean-squared variation (standard deviation) in the roughness. This RMS value should be specified by the laminate manufacturer. If you’re designing for high speed, and you need impedance controlled routing, then your manufacturer should be able to supply these values for you. For modelling, you’ll need to use the right model to describe roughness; take a look at this article in Signal Integrity Journal for more information.
If you’re working at extreme high speeds/high frequencies with low signal levels, and you require highly accurate interconnect characterization, then your best bet is to create a test coupon and use a standard measurement to determine the effective dielectric constant. Your test method should use a geometry that closely matches your intended interconnect geometry. This takes some work on the front end, but accurate test and measurement could save you unnecessary prototyping runs on the back end.
When you’re selecting from a range of PCB core vs. prepreg materials, the layer stack manager in Altium Designer® can be a huge help. You’ll have access to a materials library that contains important data on a broad range of standardized materials, or you can specify specific material properties for exotic substrate materials. These features increase your productivity while still allowing you to adapt your design to highly specific applications.
Now you can download a free trial of Altium Designer and learn more about the industry’s best layout, simulation, and production planning tools. Talk to an Altium expert today to learn more.