Orificios metalizados en tarjetas multicapa
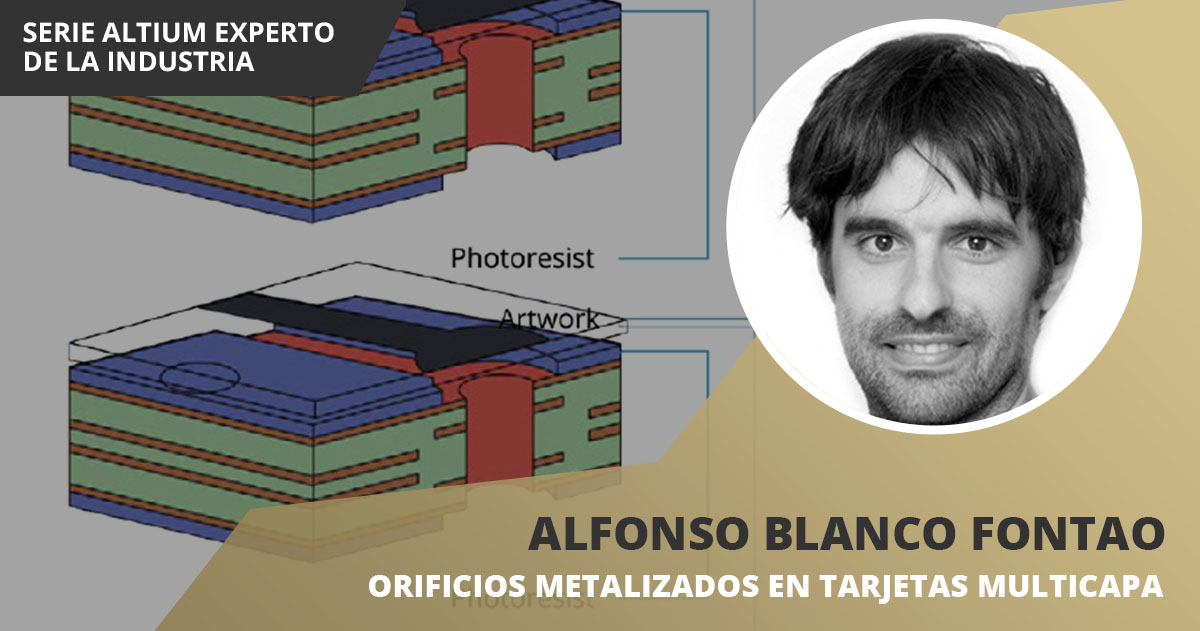
Para poder tomar decisiones acertadas de diseño, necesitamos conocer los procesos involucrados en la creación de un orificio metalizado en nuestro PCB. Los explicamos a continuación.
Taladro del Orificio
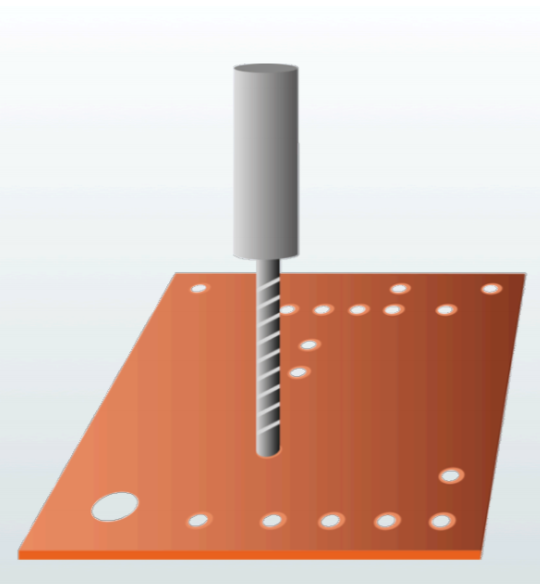
El primer paso y más obvio de todos: sirviéndonos de una broca y un taladro y con control CNC, producimos el orificio de lado a lado del PCB. En este punto tenemos, pues, un orificio no metalizado (aún) que atraviesa nuestro PCB multicapa.
Desbarbado (deburring)
Por acción del taladrado, se generan rebabas en las láminas de cobre. Son eliminadas mediante este proceso, que consiste en un cepillado de la superficie del orificio.
Desmearing
Como consecuencia de la fricción del taladrado, se produce una subida de temperatura en el interior de la tarjeta. Parte del material interno de la misma es resina de epoxy, la cual se funde y se expande a lo largo del orificio, evitando un buen contacto entre las láminas de cobre y la pared del orificio cuando produzcamos la metalización. Con el desmearing se elimina esa resina fundida, ya sea a través de un tratamiento de plasma o por medio de un proceso químico.
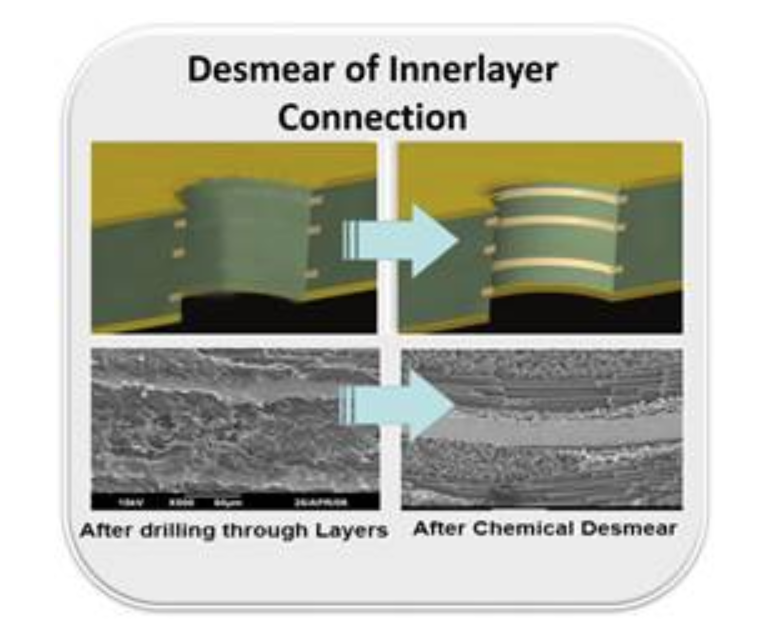
Etchback
Como paso adicional optativo, a aquellas tarjetas que requieren más fiabilidad se les aplica un proceso de etchback. Se trata de ir un paso más allá que con el desmearing y, además de eliminar el epoxy no deseado, se fuerza al material dieléctrico a retraerse ligeramente en dirección opuesta al orificio, de tal forma que el cobre sobresalga. Así, cuando se produzca la metalización, lograremos un mejor contacto (three-point connection). Se consigue mediante procesos químicos o de plasma, al igual que el desmearing.

Deposición de cobre no electrolítico
Se trata de un proceso preparatorio para la metalización electrolítica. Sumergiendo el laminado en una solución se consigue que una delgada película de cobre se deposite sobre las paredes del orificio por intercambio de iones.
Si quisiéramos metalizar por completo el orificio mediante un proceso no electrolítico, nos llevaría muchas horas, motivo por el cual es inviable. Sin embargo, es un método muy adecuado para adherir una fina capa de cobre a una superficie no metalizada aún (como es el caso en este punto). Este cobre servirá de base más adelante durante el proceso electrolítico (donde se añade espesor a la metalización). Como alternativa al cobre, se puede usar carbono o grafito.
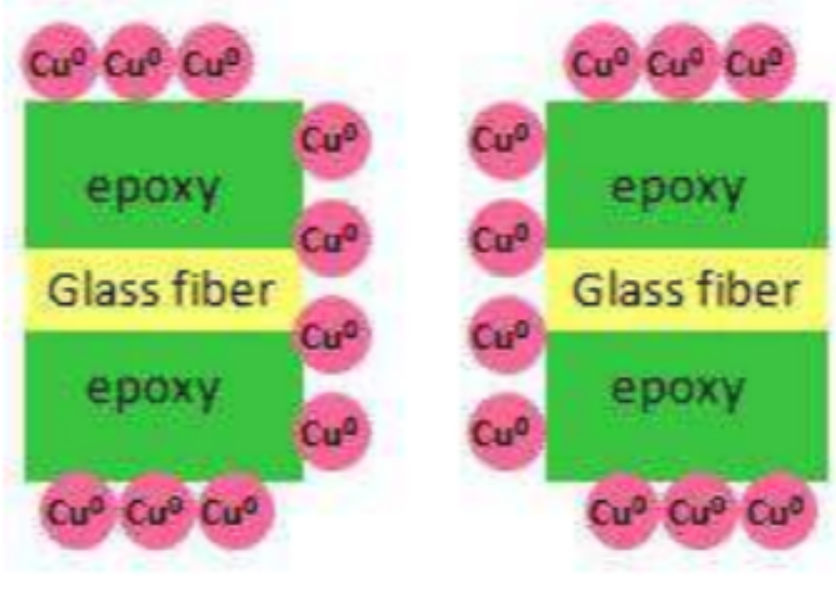
Aplicación de la capa fotoprotectora de película seca
Cubrimos las capas externas del laminado con una película fotoprotectora que será revelada.
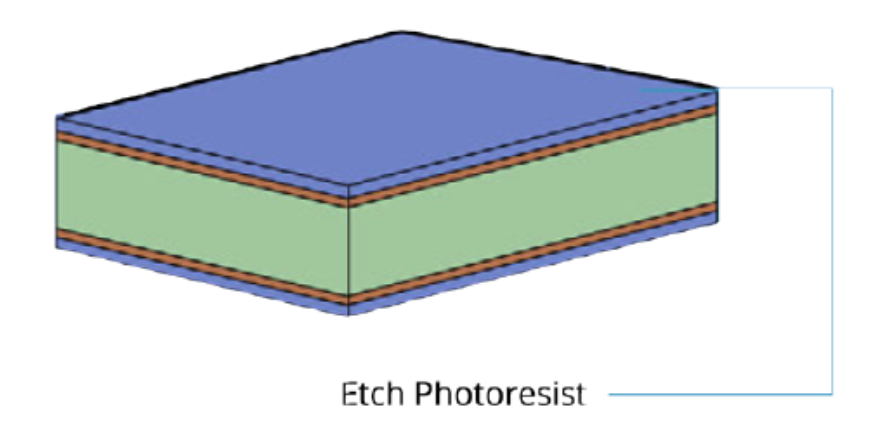
Exposición del patrón conductivo (artwork)
Al igual que haríamos con técnicas fotográficas, transferimos el patrón conductivo en negativo a la capa fotoprotectora (exponiéndolo a luz ultravioleta) y lo revelamos. En este punto, tendríamos todo el cobre no deseado (y que eliminaremos más adelante en el proceso de grabado), protegido por la película fotoprotectora. En esas superficies no habrá adhesión de metal cuando procedamos a la metalización.
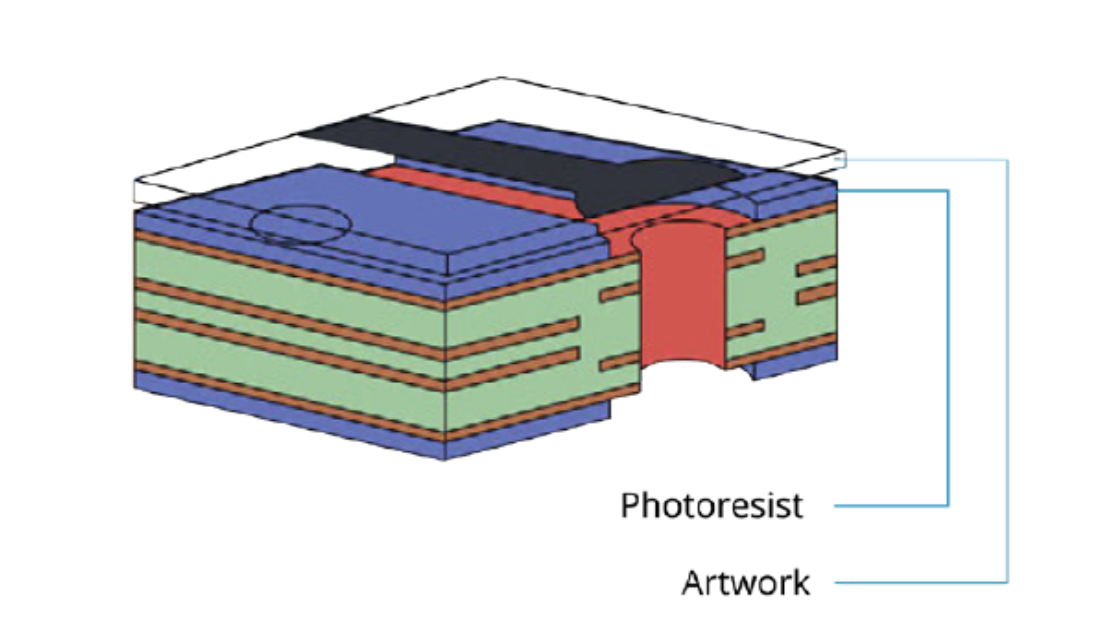
Metalización electrolítica
Es el proceso principal mediante el cual depositamos una capa de aproximadamente 25 micras (para IPC clase 3, puede ser menor para otras clases) de cobre en las paredes de los orificios. También habrá deposición en aquéllas áreas no cubiertas por la película fotoprotectora. Como su propio nombre indica, es un proceso electrolítico: sólo se deposita cobre en aquellos lugares donde podemos hacer circular una corriente eléctrica (o, dicho de otro modo, previamente metalizados). Así se explica la necesidad de la deposición de cobre no electrolítico como paso previo.
La tarjeta se introduce en agua destilada cargada negativamente. Al mismo tiempo, se rellena otro recipiente con agua y partículas de cobre, y se conecta al positivo de la fuente de energía. Se fuerza así una corriente eléctrica que llevará el cobre flotante a las zonas por donde ésta circula.
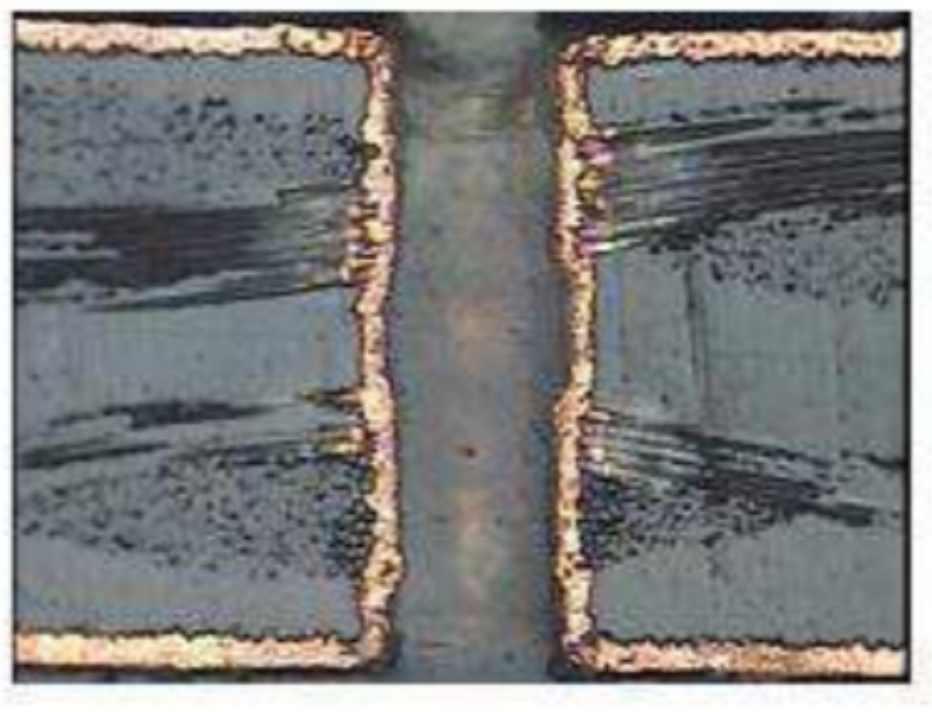
Aplicación de la capa resistiva metálica
Se añade encima de las áreas de cobre metalizadas electrolíticamente. Su función es la de evitar que dicho cobre sea eliminado en el proceso de grabado (etch).
Eliminación de la capa fotoprotectora de película seca
En este paso, volvemos a dejar desprotegido el cobre a ser eliminado en el grabado.
Grabado (etch) de las capas externas
Sumergiendo la tarjeta en una solución ácida (aunque la tecnología ya permite también usar soluciones alcalinas), conseguimos que el cobre no protegido por la capa resistiva metálica sea eliminado. Es así como transferimos el patrón de huellas, pistas, planos, etc. que hemos diseñado con nuestra herramienta CAD/CAE a la tarjeta real.
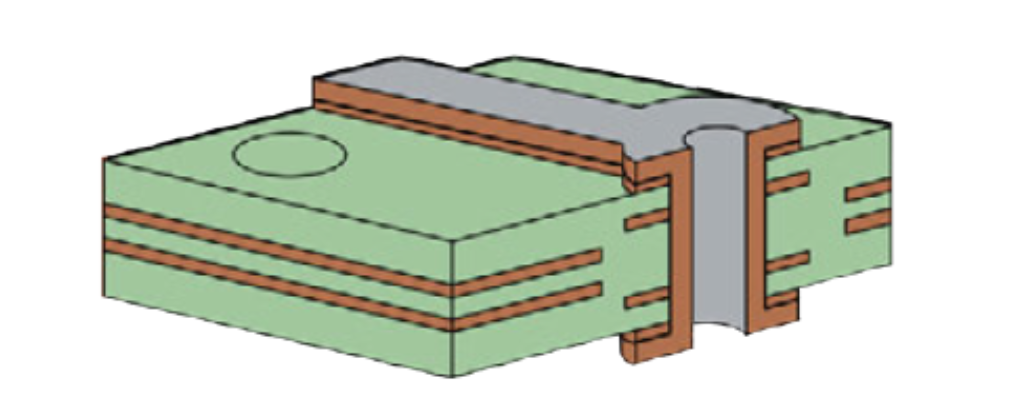
Eliminación de la capa resistiva metálica
Retiramos la protección sobre el cobre que debía permanecer en la solución ácida.
Aplicación de la máscara antisoldadura
Cubrimos toda la superficie de la tarjeta, con excepción de los pads superficiales, con máscara antisoldadura, según los ficheros de fabricación.
Aplicación del acabado de superficie
Como paso final, damos el acabado elegido por el diseñador al cobre que queda expuesto al aire. HASL (Hot Air Solder Levelling) o ENIG (Electroless Nickel Gold) son las opciones más usadas, aunque existen otras opciones igualmente plausibles. Una explicación en detalle se puede encontrar en este fenomenal artículo del experto en la industria Juan Carlos Oca.
Conclusiones
Hemos conseguido así entender por qué en las capas exteriores de cobre de nuestra tarjeta siempre tenemos un grosor de cobre mayor del de la lámina. Como norma general, se añaden 1.4 veces el cobre depositado en las paredes del orificio. A las 18 o 35 micras habituales, debemos añadir unas 35 micras (1.4x25) provenientes de este proceso. Los espesores de cobre más habituales en capas exteriores suelen ser respectivamente entorno a 35 ó 53 micras respectivamente.
Es igualmente importante mencionar una capacidad que define a los fabricantes: la relación de aspecto entre el grosor final de la tarjeta y el orificio metalizado más pequeño que pueden realizar. Es fácil deducir ahora el motivo por el que, a mayor espesor final de la tarjeta, mayor ha de ser el diámetro del orificio más pequeño: necesitamos hacer circular un fluido a su través. Si la longitud del orificio es grande y su diámetro pequeño, no podríamos llegar a metalizar la parte central del cilindro.
Otra importante conclusión que se extrae de aquí es que el diámetro del orificio final es siempre menor que el del orificio taladrado, puesto que hemos añadido entorno a 25 micras de metal en la pared del orificio.