Pianificazione iniziale DFM per i vostri PCBs
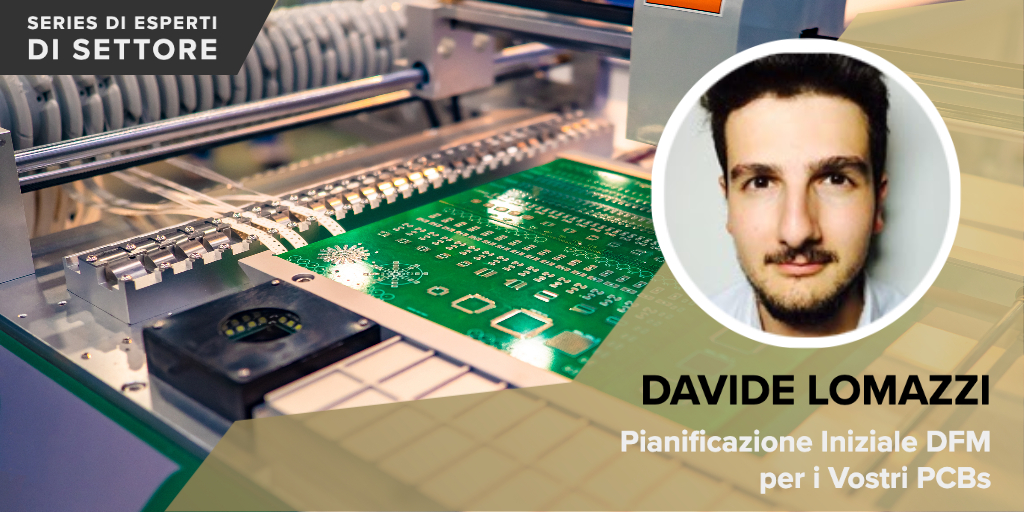
I primi passaggi da considerare quando si vuole passare da un prototip PCB ad un prodotto finito.
Diciamo che avete realizzato il vostro prototipo PCB con successo. Ora che siete sicuri che funziona e avete testato le sue funzionalità volete produrre il vostro PCB su larga scala. Quello di cui vi andrò a parlare in questo articolo sono delle considerazioni che dovreste fare sulla DFM, Design For Manufacture.
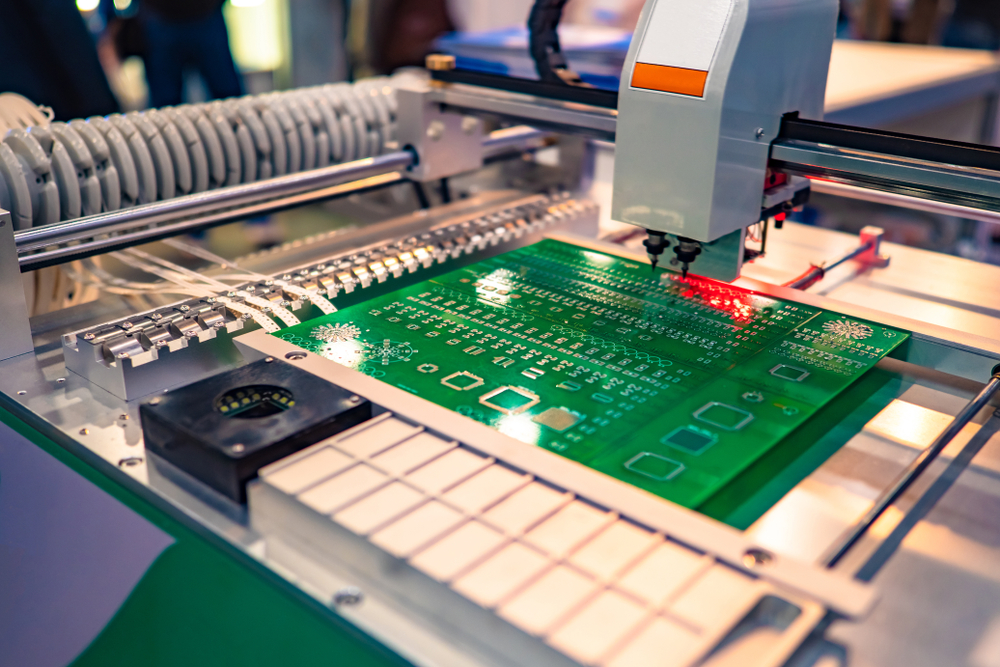
Classificazione del PCB
Secondo gli standard comuni, i circuiti stampati sono divisi in base alle performance e affidabilità che devono garantire.
Ci sono 3 classi (performance classes) dove vengono raggruppate le diverse categorie di prodotti:
- Classe 1
I circuiti di classe 1 sono quelli meno affidabili come i giocattoli. Infatti se uno di questi circuiti si rompe o è malfunzionante non ci saranno conseguenze gravi. Il vostro scopo come designer per la DFM è quello di abbassare i costi il più possibile.
- Classe 2
In classe 2 si trovano tutti quei prodotti che devono garantire un utilizzo ininterrotto per un periodo di tempo prolungato anche 10 anni. Se uno dei vostri prodotti fallisce è generalmente non accettabile.
- Classe 3
In questa categoria i PCBs non possono fallire. Sono inclusi tutti quei circuiti che svolgono funzioni critiche come alcuni apparati medicali o automotive. In questa classe è solitamente necessario fare una DFM approfondita per valutare quali sono le tecnologie di produzione e di design da utilizzare. Se uno di questi prodotti è malfunzionante ci possono essere conseguenze legali.
Gli standard di produzione e assemblaggio per la realizzazione di circuiti stampati sono gestiti dalla associazione commerciale IPC. Negli standard IPC come IPC-2221B vengono discussi molti aspetti per la DFM di PCB oltre ad usare le tre classi citate qui sopra vengono usati tre livelli di producibilità.
I livelli sono A, B e C dove A è definito come il livello di producibilità preferito, B quello standard mentre C quello ridotto con generalmente più alti costi e più scarti durante la produzione.
I livelli di producibilità possono essere differenti per diverse aspetti dei vostri PCB ad esempio potete usare un livello C per le tolleranze dei vias e un livello B le distanza tra due piste.
Pannelli di assemblaggio
Gli assembly pannels o pannelli di assemblaggio sono uno di quegli aspetti che alcuni designer tendono a non considerare all’inizio del progetto. La scopo primario di un pannello di assemblaggio è quello di velocizzare l’assemblaggio con macchine pick and place e macchine industriali per la saldatura di PCBs come reflow ovens oppure wave soldering gestendo più PCB contemporaneamente e usando formati di dimensioni standard più adatti per le macchine.
L’aspetto fondamentale che voi e il vostro team dovete conoscere sono le dimensioni dei pannelli e le dimensioni del vostro PCB per avere una idea di quanti PCB potete ottenere per ogni pannello. I pannelli hanno forma rettangolare, ci sono diversi standard e variano a seconda del vostro assemblatore.
Quando si guardano ai costi di produzione di PCB il vostro scopo è quello di minimizzare gli scarti di materiale per parti inutilizzate del pannello di assemblaggio. I pannelli di assemblaggio vengono solitamente tagliati dai pannelli dai pannelli di fabbricazione questi ultimi hanno spesso dimensioni molto maggiori rispetto ai primi. E’ necessaria quindi una buona comunicazione tra assemblatore, voi e produttore di PCB per la pianificazione dei vostri pannelli.
Un altro aspetto da considerare è la rimozione dei PCB dai pannelli di assemblaggio. Questo tema è critico e necessita di essere approfondito dai PCB designer.
Ad oggi le 2 tecniche più usate per la rimozione di PCB dai pannelli sono milling e V-scoring o V-cut.
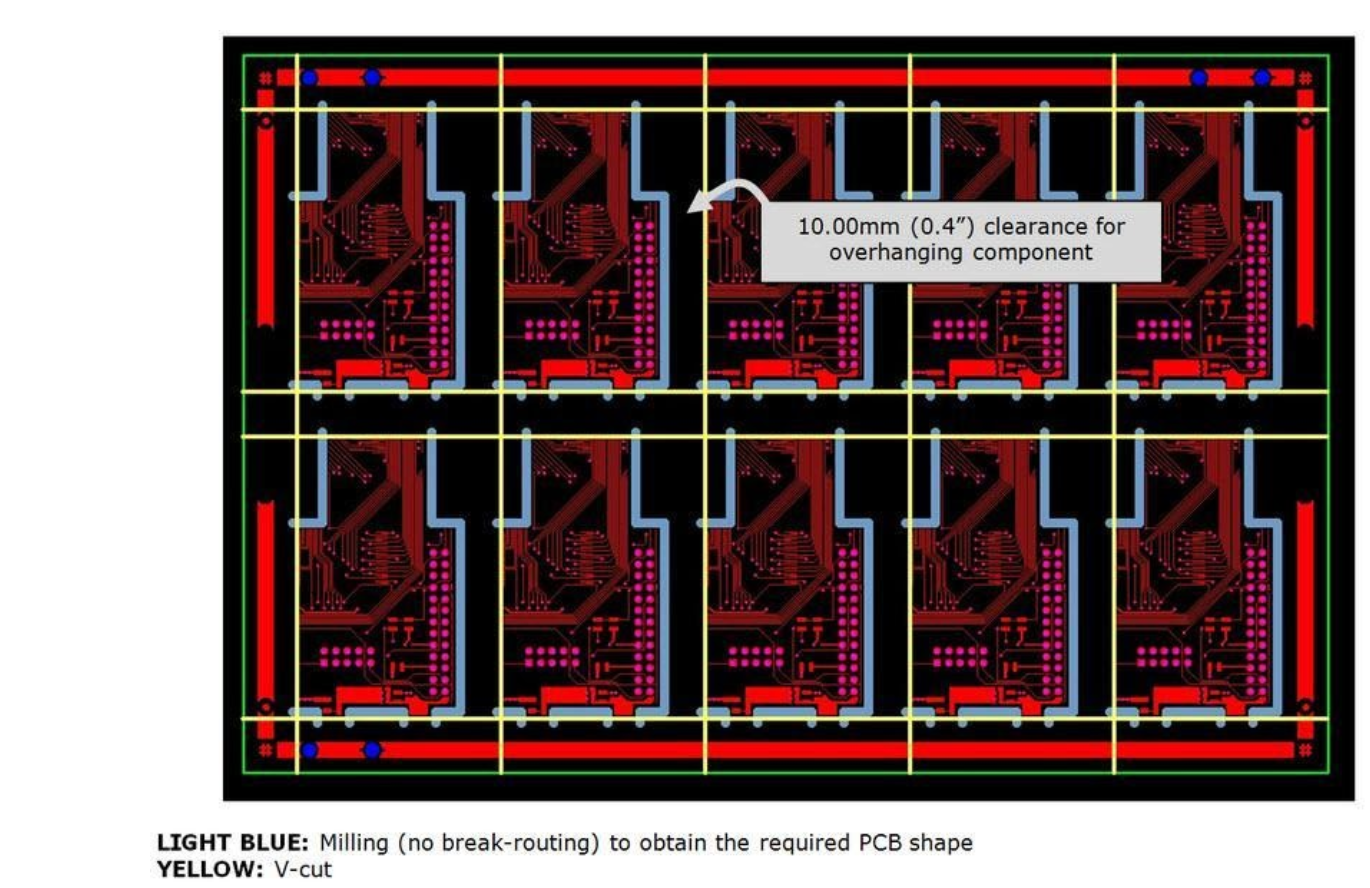
La tecnica che andrete ad utilizzare andrà ad influenzare i costi, la finitura dei bordi dei pcb e la distanza minima dei componenti dai bordi della scheda. V-scoring è solitamente più economico e veloce mentre milling permette una maggiore flessibilità per forme geometriche più complesse. Alcune volte anche differenti tecniche di taglio possono essere impiegate per lo stesso PCB.
Processi di saldatura e posizionamento dei componenti
Il posizionamento dei componenti è la responsabilità principale di un PCB designer. Quando i componenti sono posizionati correttamente avrete buone basi per tracciare efficacemente le piste e facilitare l’assemblaggio dei componenti.
I componenti through-hole (TH) sono componenti più complessi per la saldatura industriale su larga scale, il vostro primo obiettivo è quello di eliminare o ridurre il loro numero il più possibile negli schematici.
Un metodo usato per alcune schede non troppo complesse è il posizionamento di tutti i componenti SMD su un unico lato ad esempio sul lato superiore e i componenti THT (se presenti) tutti sul lato inferiore. In modo ridurrete i passaggi necessari per l’assemblaggio dei componenti. Come secondo obiettivo dovete pianificare su quali lati posizionare i vari tipi di componenti tenendo in considerazione l’altezza massima che possono raggiungere.
Ci sono diverse macchine per la saldatura, le più comuni si chiamano reflow ovens e wave soldering che presentano limitazioni.
Oltre a non potere saldare componenti through-hole (senza il loro riempimento) le macchine reflow possono danneggiare alcuni componenti delicati se i profili di temperatura sono eccessivamente lunghi o troppo elevati. Un’altra limitazione può essere l’altezza massima consentita ad esempio 24 mm and 6 mm sul lato inferiore nel caso il PCB deva passare 2 volte nella macchina.
Per quando riguarda la saldatura wave soldering questa tecnica necessita di accorgimenti specifici alcuni componenti non supportano questo metodo perchè l’onda può rovinare il package dei componenti con la sua temperatura. I componenti possono inoltre essere più proni a difetti come ponti tra due pads o residui di materiale saldante sotto i componenti.
Una corretta orientazione può migliorare le performance riducendo gli scarti e quindi i costi di produzione, la figura illustra un esempio:
Altri tipi di montaggio comunemente utilizzati nell'industria elettronica che potete considerare sono press fit e selective soldering. Queste tecnologie hanno anch'esse vantaggi e svantaggi come maggiori distanza, una dettagliata analisi ingegneristica è necessaria per valutare costi e benefici.
Conclusione
La pianificazione delle vostre schede elettronica è uno degli aspetti chiave per riuscire a sviluppare un prodotto competitivo. Una buona comunicazione iniziale e una dettagliata pianificazione sono i punti chiave per evitare errori che potrebbero richiedervi maggiori tempi per redesign di schede successivamente.
Buon lavoro.